Calcined Petroleum Coke as Carbon Raiser for Monolithic Refractories in Iron and Steel Industry
- Loading Port:
- Shekou
- Payment Terms:
- TT OR LC
- Min Order Qty:
- 20 m.t
- Supply Capability:
- 1000 m.t/month
OKorder Service Pledge
OKorder Financial Service
You Might Also Like
Factory Background
The factory is majorly running and operating carbon additive (pitch coke, calcined petroleum coke and anthracite), low nitrogen carbon additive, and brake pad making material. Company is the long term supplier of Sinosteel Corporation, Shanghai Carbon Corporation, the plant of SGL Group the Carbon Company in China and some largest special carbon products producing plants.
YUAI also supplies huge amout of high quality carbon additive and graphite carbon additive to steel plants, foundries and ferrotungsten plants. YUAI has been assigned by BAO STEEL as the only organization for processing pitch coke for export purpose. The group’s major products are constantly exported to Japan, Korea, Malaysia, South East Asia countries, Europe and America, which receive praises by our consumers.
The group has invested numbers of calcinators in Anhui China to ensure the capability of producing and processing huge amount of carbon additive. Further investment is on process. According to the orders from customers, YUAI is able to processing and providing different specifications of carbon additive and other products. To provide best quality of products and to offer customers most satisfied service is YUAI’s operating objectives.
Calcined Petroleum Coke
FC:98.5%min,
S:0.5%max
A:0.8%max
V:0.7%max
Mositure:0.5%max
Size:1-5mm
This product is mainly used in steel-making and foundry. Calcined Petroleum Coke
Calcined Petroleum Coke comes from delayed coke which extracted from oil refinery. Although Calcined Petroleum Coke contains a little bit higher level of sulfur and nitrogen than pitch coke, the price advantage still makes it widely used during steel-making and founding as a kind of carbon additive/carburant.
Technology:
Laborary Equpment
In our lab,we has a high precision balance,mullfe furnace,sample making machine, dring box,sulfur measurement instrument and other calibratiing equipments.As a result,before deliverung to our customers,our products have to pass a strict test to ensure the quality and components.The testing reports will be sent to our customers to confirm untill they satisfy with it.
Packaging & Delivery
Packaging Detail:25kg paper bag into 1t weaving bag 5kg, 10kg and 20kg weaving bag into 1t weaving bag 25kg weaving bag put on pallet covered with entanglement wrap product direct into packing bag 25kg paper bag put on pallet covered with entanglement Wrap 25kg weaving bag into 1t weaving bag.
Delivery Details: 7 days
- Q: How do monolithic refractories impact the quality of iron and steel products?
- The quality of iron and steel products is greatly influenced by monolithic refractories. These refractories are extensively used in the lining of furnaces and other high-temperature environments where iron and steel undergo processing. To begin with, monolithic refractories play a vital role in insulating and safeguarding the furnace lining from the intense heat generated during the manufacturing of iron and steel. By maintaining the desired temperature, these refractories ensure consistent and proper heating of the metal, thereby achieving the desired product quality. Inadequate insulation would result in significant heat loss, leading to inefficient energy consumption and inconsistent product quality. Additionally, monolithic refractories have a significant impact on the overall cleanliness of iron and steel. During the production process, impurities and slag are formed, which can contaminate the metal if not managed properly. Refractories with high resistance to slag penetration and corrosion prevent these impurities from infiltrating the metal, ensuring a cleaner and purer final product. Moreover, monolithic refractories also contribute to the mechanical strength and durability of the furnace lining. The lining must withstand the harsh conditions and repeated thermal shocks encountered during the production process of iron and steel. A sturdy and well-designed refractory lining can resist cracking, spalling, and erosion, thereby prolonging the furnace's lifespan and reducing the risk of downtime. In conclusion, monolithic refractories have a profound impact on the quality of iron and steel products. They provide thermal insulation, prevent contamination, and ensure the mechanical integrity of the furnace lining. Manufacturers can optimize their production processes, enhance product quality, and improve overall operational efficiency by selecting the appropriate refractory material and maintaining it correctly.
- Q: What are the factors influencing the choice of monolithic refractories for different furnace types?
- There are several factors that influence the choice of monolithic refractories for different furnace types. Firstly, the operating temperature of the furnace is a crucial factor as different monolithic refractories have different temperature resistance levels. Secondly, the type of material being processed in the furnace is important as certain materials may require specific refractories to withstand their corrosive or abrasive nature. Thirdly, the furnace design and its heating method also play a role in determining the suitable refractory material. Additionally, the thermal conductivity, thermal shock resistance, and mechanical strength of the refractory are considered to ensure optimal performance and durability. Finally, cost, availability, and installation requirements are factors that can influence the choice of monolithic refractories for different furnace types.
- Q: How do monolithic refractories respond to changes in thermal conditions?
- Monolithic refractories have the ability to withstand and adapt to changes in thermal conditions. They have a high thermal shock resistance, meaning they can handle rapid changes in temperature without cracking or breaking. Additionally, they exhibit good thermal conductivity, allowing them to efficiently conduct and distribute heat. Overall, monolithic refractories demonstrate a stable and reliable response to changes in thermal conditions.
- Q: What are the recommended drying procedures for monolithic refractories?
- Drying methods for monolithic refractories differ based on the specific type and composition of the material. Nevertheless, there exist general guidelines that can be adhered to. Initially, it is crucial to eliminate any excess moisture from the refractory material prior to drying. This can be achieved by storing the refractory in a dry environment or utilizing a dehumidifier if necessary. Once the refractory material has been adequately dried, the drying process can commence. It is advisable to initiate the process with a low drying temperature in order to prevent cracking or spalling. Gradually raising the temperature over time will allow for the gradual release of moisture. This can be accomplished by employing a controlled drying oven or furnace. The duration of the drying process will differ depending on the thickness and composition of the refractory. It is imperative to adhere to the manufacturer's guidelines for the specific refractory material being utilized, as they will provide the recommended drying duration and temperature range. Throughout the drying process, it is important to closely monitor the refractory for any indications of cracking or spalling. Should any cracks or damage occur, the drying process should be immediately halted to prevent further harm. It may be necessary to repair or replace the damaged areas before proceeding with the drying process. Once the refractory material has been fully dried, it is crucial to gradually cool it down to avoid thermal shock. This can be achieved by gradually reducing the temperature over time or allowing the refractory to naturally cool in a controlled environment. In conclusion, the recommended drying procedures for monolithic refractories involve gradually increasing the temperature over time, closely monitoring for any signs of damage, and slowly cooling down the refractory to prevent thermal shock. It is essential to adhere to the manufacturer's guidelines and recommendations for the specific refractory material being utilized to ensure proper drying and optimal performance.
- Q: How are monolithic refractories installed and repaired in iron and steel applications?
- To ensure optimal performance and longevity in iron and steel applications, specific procedures are employed for the installation and repair of monolithic refractories. The installation process typically involves the following steps: 1. Proper surface preparation is crucial. This entails removing loose material, dirt, and dust to create a smooth and clean substrate that facilitates good adherence of the refractory material. 2. The refractory material, supplied as dry powders or granules, is mixed with water or a specific bonding agent according to the manufacturer's instructions to achieve the desired properties. 3. The mixed refractory material is then applied to the prepared surface using techniques such as troweling, spraying, or casting, depending on the installation requirements and the type of monolithic refractory. 4. Curing is necessary to maximize the strength and durability of the refractory material. The curing process can involve air drying, heat treatment, or a combination of both, in accordance with the specific refractory material's recommendations. When it comes to repairing monolithic refractories in iron and steel applications, the following steps are generally followed: 1. Thorough assessment of the damaged area or component is conducted to determine the extent of the damage and the appropriate repair method. 2. The damaged monolithic refractory material is carefully removed using suitable tools and techniques while ensuring the underlying substrate remains intact. 3. Similar to the installation process, the surface where the repair will take place is cleaned and prepared by removing any loose material, dirt, and dust. 4. The repair material, typically the same or similar to the original monolithic refractory, is mixed and applied to the damaged area. The application method may vary depending on the nature of the repair and the specific requirements of the refractory material. 5. The repaired area is properly cured and inspected to ensure the quality and effectiveness of the repair, following the manufacturer's guidelines for curing and post-repair inspection procedures. In conclusion, the meticulous execution of surface preparation, proper mixing and application of refractory material, and appropriate curing procedures are essential for the installation and repair of monolithic refractories in iron and steel applications. These steps guarantee reliable and durable refractory linings, which are vital for the efficient operation of iron and steel processes.
- Q: Can monolithic refractories be used for the lining of ladle refining furnaces and VOD converters?
- Indeed, ladle refining furnaces and VOD converters can benefit from the utilization of monolithic refractories. These refractories, which consist of a single, uniform material, can be molded and installed in various settings, particularly those involving extreme temperatures such as ladle refining furnaces and VOD converters. The advantage of monolithic refractories lies in their simplicity of application and repair. They can be either cast or gunned in place, offering flexibility in terms of lining design and installation. The lining of ladle refining furnaces and VOD converters requires materials capable of withstanding high temperatures, chemical reactions, and mechanical stresses. Monolithic refractories are well-suited for these demanding applications due to their exceptional resistance to thermal shock and chemical attack. In the case of ladle refining furnaces, monolithic refractories are used to line the vessel in which molten metal is contained and processed. By doing so, these refractories help to maintain the desired temperature and safeguard the ladle from the corrosive effects of both molten metal and slag. Additionally, they serve as insulation to minimize heat loss and enhance energy efficiency. VOD converters, on the other hand, are employed in the steelmaking process to reduce the carbon content of molten steel. Monolithic refractories play a crucial role in lining the converter's vessel and ensuring the maintenance of the required temperature for the decarburization reaction. Furthermore, they provide protection against the corrosive impact of molten metal and slag, thereby guaranteeing the converter's durability and performance. To summarize, monolithic refractories possess outstanding characteristics that make them an excellent choice for lining ladle refining furnaces and VOD converters. Their versatility, ease of installation, and ability to withstand high temperatures and chemical attack render them perfectly suited for these critical applications within the steel industry.
- Q: How do monolithic refractories resist corrosion and erosion in iron and steel applications?
- Monolithic refractories, unlike traditional refractory bricks, consist of a single, homogeneous material and are highly resilient and effective in combating corrosion and erosion in iron and steel applications. Their monolithic nature provides several advantages when it comes to corrosion and erosion resistance. One key advantage is their low porosity, which prevents corrosive agents like molten metal or slag from infiltrating the refractory structure. By minimizing interconnected pores, monolithic refractories significantly reduce the likelihood of chemical reactions that cause corrosion. Moreover, monolithic refractories exhibit excellent resistance to thermal shock, a common issue in iron and steel applications due to rapid temperature changes. Their high thermal conductivity and low thermal expansion enable them to withstand thermal shock without compromising their integrity. This characteristic allows them to resist erosion caused by the flow of molten metal or slag. Additionally, monolithic refractories are highly durable and possess good mechanical strength, enabling them to withstand the abrasive forces often encountered in iron and steel applications. The intense mechanical impact, vibrations, and abrasive wear experienced in these environments can be effectively resisted by monolithic refractories, ensuring their longevity and reliability. In conclusion, monolithic refractories are the preferred choice for lining furnaces, ladles, and other equipment used in the production of iron and steel due to their resistance to corrosion and erosion. Their low porosity, excellent resistance to thermal shock, and high mechanical strength make them an ideal option for these demanding applications.
- Q: What are the factors to consider when selecting monolithic refractories for specific applications?
- When selecting monolithic refractories for specific applications, several factors need to be considered. These include the operating temperature, chemical composition of the material being processed, mechanical stresses, thermal cycling, and the presence of any corrosive or erosive agents. Additionally, the refractory's thermal conductivity, porosity, density, and its ability to resist thermal shock and spalling are crucial factors to take into account. The availability and cost of the refractory material, as well as the installation and maintenance requirements, should also be considered during the selection process.
- Q: How are monolithic refractories different from traditional refractory materials?
- Monolithic refractories are different from traditional refractory materials in several ways. Firstly, while traditional refractory materials are typically made from bricks, blocks, or tiles, monolithic refractories are composed of a single, continuous material. This means that they do not have any joints or seams, which can be a weak point in traditional refractory structures. Secondly, monolithic refractories are much easier to install compared to traditional refractory materials. They can be easily shaped and applied in situ, allowing for greater flexibility in design and construction. In contrast, traditional refractory materials require skilled labor and more time-consuming installation methods such as bricklaying. Furthermore, monolithic refractories offer improved thermal shock resistance. Due to their continuous structure, they can better withstand sudden changes in temperature without cracking or spalling. Traditional refractory materials, on the other hand, may be more susceptible to thermal shock damage. Another advantage of monolithic refractories is their ability to provide better insulation. Their composition often includes lightweight aggregates or insulating fibers, which help to reduce heat loss and improve energy efficiency. Traditional refractory materials, while still capable of providing insulation, may not offer the same level of thermal efficiency. Lastly, monolithic refractories have the advantage of being more cost-effective. Their ease of installation, reduced labor requirements, and improved thermal performance contribute to lower overall project costs compared to traditional refractory materials. In summary, monolithic refractories differ from traditional refractory materials in terms of their continuous structure, ease of installation, improved thermal shock resistance, better insulation properties, and cost-effectiveness. These characteristics make them a preferred choice in many industries where high-temperature applications and thermal insulation are required.
- Q: How do monolithic refractories improve energy efficiency in the iron and steel industry?
- Monolithic refractories play a crucial role in improving energy efficiency in the iron and steel industry through various mechanisms. Firstly, these refractories have excellent insulation properties, which help in reducing heat loss during the production process. By minimizing heat loss, monolithic refractories ensure that more heat is retained within the furnace, resulting in higher energy efficiency. Moreover, monolithic refractories have low thermal conductivity, allowing for better heat transfer within the furnace. This means that the heat generated during the production process can be efficiently distributed throughout the furnace, enabling optimal temperature control and reducing energy wastage. In addition, monolithic refractories have high resistance to thermal shock and corrosion, which are common challenges in the iron and steel industry. By withstanding extreme temperatures and chemical reactions, these refractories prevent premature wear and tear, thus reducing the need for frequent repairs and replacements. This not only saves energy but also minimizes downtime, leading to increased productivity and energy efficiency. Furthermore, the use of monolithic refractories allows for better furnace design and optimization. Their flexibility enables the creation of custom shapes and linings that suit specific furnace requirements, resulting in improved heat transfer and combustion efficiency. This customized approach promotes energy savings by maximizing the utilization of fuel and reducing emissions. Lastly, monolithic refractories have a longer lifespan compared to traditional brick refractories. This prolonged durability reduces the frequency of refractory replacements, resulting in lower energy consumption associated with the manufacturing and installation of new refractories. Overall, monolithic refractories contribute significantly to energy efficiency in the iron and steel industry by reducing heat loss, improving heat transfer, withstanding thermal shock and corrosion, enabling better furnace design, and increasing refractory lifespan. Their use not only saves energy but also enhances productivity and sustainability within the industry.
Send your message to us
Calcined Petroleum Coke as Carbon Raiser for Monolithic Refractories in Iron and Steel Industry
- Loading Port:
- Shekou
- Payment Terms:
- TT OR LC
- Min Order Qty:
- 20 m.t
- Supply Capability:
- 1000 m.t/month
OKorder Service Pledge
OKorder Financial Service
Similar products
Hot products
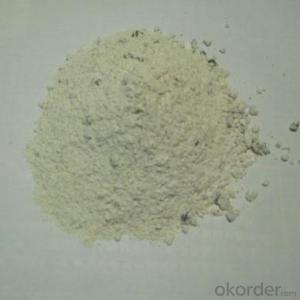
Monolithic Refractories for Iron and Steel Industry - Acid Ramming Mass for Induction Furnace Lining
Hot Searches
Related keywords