Monolithic Refractories for Iron and Steel Industry:High Alumina Raw Bauxite Products
- Loading Port:
- Qingdao
- Payment Terms:
- TT OR LC
- Min Order Qty:
- 400 m.t.
- Supply Capability:
- 5000 m.t./month
OKorder Service Pledge
OKorder Financial Service
You Might Also Like
Specifications
raw bauxite
1. Producing for 20 years.
2. refractory and abrasive
3. Competitive price
4. Al2O3 95%min
It is made by electric arc furnace melting under high temperature of 1100 degrees to 1400 degrees with the raw material of bauxite, anthracite and scrap iron. The main ingredient is AL2O3. With its high micro hardness of 1800-2200kg/mm2, it has many uses like abrasives and refractory. This kind of product has two types P sand and F sand with different uses。
Application:
1. Be used in polishing, grinding.
2. Suitablefor making grinding wheel, cutting, wheel, grinding disc.
3. Its high hardness and abrasion adapt to abrasive tools.
4. For advanced refractory materials
Application | Model | Al2O3 | Na2O | Fe2O3 | SiO2 | TiO2 | LOI | True density | a-Al2O3 | D50 | Particle size | specific surface |
Unit | ≥ % | ≤% | ≤% | ≤% | ≤% | ≤% | g/m3 | ≥ % | um | um | m2/g | |
Dry pressing/CIP series | TCH-101 | 99.7 | 0.08 | 0.02 | 0.018 | 0.006 | 0.15 | 3.96 | 96 | 75 | 2--3 | 0.6-0.8 |
TCH-102 | 99.6 | 0.1 | 0.02 | 0.018 | 0.006 | 0.15 | 3.95 | 95 | 75 | 2--3 | 0.6-0.8 | |
TCH-103 | 99.5 | 0.2 | 0.02 | 0.018 | 0.006 | 0.2 | 3.95 | 95 | 75 | 2--3 | 0.8-1.0 | |
TCH-105 | 99.4 | 0.3 | 0.02 | 0.018 | 0.006 | 0.2 | 3.93 | 93 | 75 | 2--3 | 0.8-1.0 | |
Injection moulding | TCH-213 | 99.5 | 0.15 | 0.02 | 0.018 | 0.006 | 0.15 | 3.95 | 95 | 75 | 3-4 | 0.5-0.6 |
TCH-211 | 99.7 | 0.1 | 0.02 | 0.018 | 0.006 | 0.1 | 3.96 | 96 | 75 | 3-5 |
- Q: How do monolithic refractories contribute to energy efficiency in iron and steel production?
- Monolithic refractories contribute to energy efficiency in iron and steel production by providing superior insulation and heat containment properties. These refractories have low thermal conductivity, which minimizes heat loss and ensures that the intense temperatures required for the production process are maintained within the furnace or kiln. This reduces the need for excessive fuel consumption and enables more efficient use of energy resources. Additionally, monolithic refractories can withstand high temperatures without significant structural damage, prolonging their lifespan and reducing the frequency of replacement, further contributing to energy efficiency in the industry.
- Q: How do monolithic refractories enhance the performance and longevity of furnaces?
- Monolithic refractories play a crucial role in enhancing the performance and longevity of furnaces. These specialized materials are designed to withstand high temperatures, extreme thermal shock, and harsh chemical environments, making them ideal for lining furnaces. Firstly, monolithic refractories provide excellent insulation properties, ensuring minimal heat loss and maximum energy efficiency. By reducing heat loss, they help maintain a consistent temperature inside the furnace, allowing for more effective and efficient heating processes. This insulation also prevents the external environment from interfering with the internal temperature, ensuring stable and controlled heating operations. Secondly, these refractories have high resistance to thermal shock. Furnaces often undergo rapid temperature changes as they heat and cool down. Monolithic refractories are capable of handling these abrupt temperature fluctuations without cracking or spalling, thereby preserving the integrity of the furnace lining. This resistance to thermal shock also translates into improved safety, as it reduces the risk of sudden failure or damage to the furnace structure. Furthermore, monolithic refractories possess excellent chemical resistance, making them highly durable in aggressive environments. Furnaces are exposed to various corrosive gases, molten metals, and chemical reactions. The refractories' ability to withstand these harsh conditions ensures that the furnace lining remains intact and protects the underlying structure. This resistance to chemical attack also prevents contamination of the heated materials, ensuring the quality of the final product. Additionally, monolithic refractories offer easy installation and repair. Unlike traditional brick refractories, which require time-consuming and labor-intensive construction, monolithic refractories are typically cast or gunned into place, allowing for quick and efficient installation. Moreover, if any damage occurs, these materials can be easily patched or repaired, minimizing downtime and ensuring continuous furnace operation. In summary, monolithic refractories greatly enhance the performance and longevity of furnaces by providing excellent insulation, resistance to thermal shock, chemical durability, and ease of installation and repair. By choosing the appropriate monolithic refractory material for specific furnace applications, manufacturers can significantly improve furnace efficiency, maintain consistent temperatures, ensure safety, and prolong the lifespan of their furnaces.
- Q: What are the environmental considerations associated with monolithic refractories?
- The environmental considerations associated with monolithic refractories primarily revolve around their production and disposal. The manufacturing process of monolithic refractories involves high energy consumption and emissions, contributing to carbon dioxide and other greenhouse gas emissions. Additionally, some raw materials used in their production, such as silica, can have negative environmental impacts during extraction. In terms of disposal, monolithic refractories are typically difficult to recycle due to their composition and structure. As a result, they often end up in landfills, which can contribute to pollution and waste management issues. Overall, the environmental considerations associated with monolithic refractories highlight the need for sustainable manufacturing practices, improved waste management strategies, and the development of alternative refractory materials that have less negative environmental impact.
- Q: What are the advantages of using plastic refractories in the iron and steel industry?
- There are several advantages of using plastic refractories in the iron and steel industry. Firstly, plastic refractories offer excellent thermal insulation properties. They have low thermal conductivity, which means they can effectively retain heat and prevent excessive heat loss during the manufacturing process. This is crucial in the iron and steel industry as maintaining high temperatures is essential for the proper functioning of furnaces and other equipment. Secondly, plastic refractories have superior resistance to chemical attack and corrosion. They can withstand exposure to various chemicals, including molten metals and slag, without deteriorating or losing their structural integrity. This is especially important in the iron and steel industry, where materials come into contact with highly corrosive substances on a regular basis. Another advantage of plastic refractories is their ease of installation and repair. Unlike other refractory materials, plastic refractories can be easily shaped and molded into the desired form, allowing for precise fitting and quick installation. Additionally, they can be easily repaired or patched in case of damage or wear, which reduces downtime and maintenance costs. Furthermore, plastic refractories exhibit good mechanical strength and abrasion resistance. This enables them to withstand the physical stresses and mechanical forces present in the iron and steel industry, such as vibrations, impacts, and mechanical loading. Their high resistance to wear and tear ensures longevity and reduces the need for frequent replacements. Lastly, plastic refractories have a high thermal shock resistance. They can withstand rapid temperature changes without cracking or spalling. This is beneficial in the iron and steel industry, where materials are subjected to extreme temperature differentials, such as during the heating and cooling cycles of furnaces. In conclusion, the advantages of using plastic refractories in the iron and steel industry include excellent thermal insulation, resistance to chemical attack, ease of installation and repair, good mechanical strength, abrasion resistance, and high thermal shock resistance. These properties make plastic refractories an ideal choice for various applications in this industry, ensuring efficient and reliable operations.
- Q: What are the key properties of shotcrete mixes used for monolithic refractory applications?
- The key properties of shotcrete mixes used for monolithic refractory applications are: 1. High Strength: Shotcrete mixes used for monolithic refractory applications should have high compressive strength to withstand the high temperatures and stresses experienced in refractory environments. This ensures that the shotcrete lining remains intact and provides effective insulation and protection. 2. Low Porosity: Shotcrete mixes should have low porosity to minimize the infiltration of gases and liquids into the refractory lining. This helps to prevent corrosion and degradation of the lining, and ensures its long-term durability. 3. Thermal Stability: Shotcrete mixes should exhibit excellent thermal stability to withstand the extreme heat conditions in refractory applications. They should have low thermal conductivity to effectively insulate the structure and prevent heat transfer. This helps to maintain the integrity of the refractory lining and optimize its performance. 4. Abrasion Resistance: Shotcrete mixes used for monolithic refractory applications should have high abrasion resistance to withstand the mechanical wear and tear caused by the movement of materials and particles. This property ensures that the refractory lining remains intact and provides effective protection against erosion. 5. Chemical Resistance: Shotcrete mixes should be resistant to chemical attack from molten metals, slag, and other corrosive substances present in refractory applications. This helps to maintain the integrity of the lining and prolong its service life. 6. Workability: Shotcrete mixes should have good workability to facilitate easy placement and application. This allows for efficient and precise installation of the refractory lining, ensuring the desired thickness and coverage. Overall, shotcrete mixes used for monolithic refractory applications should possess a combination of high strength, low porosity, thermal stability, abrasion resistance, chemical resistance, and workability to ensure optimal performance and durability in refractory environments.
- Q: How do monolithic refractories enhance the efficiency of reheating furnaces?
- Monolithic refractories play a crucial role in enhancing the efficiency of reheating furnaces in several ways. Firstly, monolithic refractories offer excellent thermal insulation properties, which minimize heat losses from the furnace. This insulation helps to maintain a high and consistent temperature inside the furnace, reducing the need for excessive fuel consumption and improving energy efficiency. Secondly, monolithic refractories have high thermal conductivity, which allows for efficient heat transfer within the furnace. This means that the heat generated by the burners can be evenly distributed throughout the furnace, ensuring uniform heating of the materials being reheated. This uniform heating not only enhances the overall efficiency but also helps to prevent hot spots or cold spots, which can negatively impact the quality of the reheated products. Moreover, monolithic refractories have excellent resistance to thermal shock and mechanical stress. Reheating furnaces often undergo rapid temperature changes and are subjected to intense mechanical forces due to the movement of materials and the operation of various equipment. The use of monolithic refractories helps to prevent cracks, spalling, and other forms of refractory damage, thus ensuring the longevity and continuous operation of the furnace without interruptions for repairs. Additionally, monolithic refractories offer ease of installation, repair, and maintenance compared to traditional brick refractories. Their ability to be cast or sprayed onto the furnace lining allows for a more precise and seamless installation, reducing the risk of weak joints or gaps that could compromise the furnace's efficiency. Furthermore, in case of any damage or wear, monolithic refractories can be easily repaired or patched up, minimizing downtime and improving the overall productivity of the furnace. In summary, the use of monolithic refractories in reheating furnaces enhances efficiency by providing effective thermal insulation, facilitating uniform heat distribution, resisting thermal shock and mechanical stress, and allowing for easier installation and maintenance. These benefits contribute to lower energy consumption, improved product quality, increased furnace durability, and reduced operational costs.
- Q: What are some common applications of monolithic refractories in the iron and steel industry?
- Due to their superior performance and versatility, monolithic refractories find wide application in the iron and steel industry. In this industry, these refractories serve various purposes, such as: 1. Blast Furnace: To withstand high temperatures and chemical reactions, blast furnaces employ monolithic refractories in their linings. These refractories maintain the structural integrity of the furnace and provide insulation against heat loss. 2. Ladle Lining: Monolithic refractories line ladles, which transfer molten iron or steel from the blast furnace to the steelmaking process. They exhibit excellent resistance to thermal shock and erosion caused by the aggressive molten metal. 3. Tundish Lining: Tundish, an intermediate vessel that distributes molten steel to multiple casting molds, utilizes monolithic refractories in its lining. This ensures proper thermal insulation and prevents steel contamination during casting. 4. Electric Arc Furnace (EAF): The lining of EAFs, used in the steelmaking process, consists of monolithic refractories that withstand extreme temperatures and chemical reactions. They exhibit remarkable resistance to high heat and erosion caused by the molten metal and slag. 5. Induction Furnace: Monolithic refractories are also used in the lining of induction furnaces, which melt and refine metals. They provide insulation and protect the furnace structure from the high temperatures and chemical reactions occurring during the melting process. 6. Continuous Casting: Continuous casting machines require monolithic refractories in their linings to ensure smooth and consistent casting of molten steel. These refractories display excellent resistance to high temperatures, thermal shock, and erosion caused by the molten metal and slag. In summary, monolithic refractories play a crucial role in the iron and steel industry by enhancing the overall efficiency and productivity of the manufacturing process. They achieve this by providing durability, thermal insulation, and resistance to chemical reactions.
- Q: How do monolithic refractories contribute to the safety of iron and steel plants?
- The safety of iron and steel plants heavily relies on monolithic refractories. These refractories are specifically designed to withstand the harsh conditions commonly encountered in these industrial settings, including high temperatures, chemical attacks, and mechanical stresses. By using monolithic refractories, iron and steel plants can enjoy the following benefits: 1. Thermal resistance: Monolithic refractories excel in resisting extreme temperatures, preventing heat loss and ensuring the efficient operation of equipment and systems. This thermal insulation contributes to plant safety by reducing the risk of overheating, which can lead to equipment failure or catastrophic accidents. 2. Chemical resistance: Iron and steel plants involve the use of various chemicals, such as molten metal, slag, and corrosive gases. Monolithic refractories exhibit high resistance to these aggressive chemical environments, preventing corrosion, erosion, and material degradation. This resistance ensures the integrity of refractory linings, reducing the risk of leaks, spills, and contamination that could endanger workers and the environment. 3. Structural stability: Monolithic refractories provide excellent mechanical strength, offering stability to furnace linings, ladles, and other equipment. This stability is crucial for the safe operation of iron and steel plants, minimizing the risk of structural failure, collapse, or damage caused by mechanical stresses or heavy loads. 4. Quick repair and maintenance: Monolithic refractories offer easy installation and repair compared to traditional brick refractories. They can be poured, gunned, or rammed in place, allowing for swift repairs and maintenance. This rapid response to refractory failures or damages contributes to plant safety by minimizing downtime and preventing potential hazards associated with equipment malfunction. 5. Flexibility and adaptability: Monolithic refractories can be tailored to meet the specific needs of iron and steel plants. They can be customized in terms of composition, density, thermal conductivity, and other properties, ensuring optimal performance under varying operating conditions. This adaptability ensures that refractory linings are well-suited for the plant's processes, reducing the likelihood of accidents caused by inadequate refractory materials. In conclusion, monolithic refractories enhance the safety of iron and steel plants by providing thermal resistance, chemical resistance, structural stability, rapid repair capabilities, and flexibility. By utilizing these refractories, iron and steel plants can maintain a safe working environment, minimize the risk of accidents, and ensure the reliable operation of their equipment and systems.
- Q: How do monolithic refractories provide thermal insulation in the iron and steel industry?
- The iron and steel industry heavily relies on monolithic refractories for thermal insulation. These refractories are extensively used to line furnaces and other high-temperature equipment involved in the production processes. Monolithic refractories excel in thermal insulation due to their ability to withstand extreme temperatures without degradation or melting. They are specifically designed to resist high heat, enabling their usage in environments with temperatures reaching several thousand degrees Celsius. By enduring such extreme conditions, these refractories effectively prevent heat transfer to the surrounding structure, thereby ensuring insulation. Another key aspect of monolithic refractories' thermal insulation is their low thermal conductivity. These materials possess a low thermal conductivity, rendering them inefficient in conducting heat. Instead, they trap heat within their structure and minimize its transfer to the surrounding equipment or environment. This characteristic is instrumental in maintaining optimal temperatures inside furnaces and other high-temperature equipment, enabling efficient and controlled metal production. Moreover, monolithic refractories can be applied as a thick lining layer, further establishing an additional barrier between the high-temperature environment and the surrounding equipment. The thickness of the refractory lining acts as a buffer, reducing heat transfer and mitigating the impact of high temperatures on the structural integrity of the equipment. In addition to providing thermal insulation, monolithic refractories also exhibit exceptional resistance to chemical attack and mechanical wear, which are common challenges in the iron and steel industry. This resistance ensures the longevity of the refractory lining, guaranteeing consistent and reliable insulation over time. In summary, monolithic refractories contribute to thermal insulation in the iron and steel industry through their high-temperature resistance, low thermal conductivity, thick lining layer, and resistance to chemical attack and mechanical wear. These properties effectively maintain the desired temperature inside equipment and safeguard the surrounding structure from the intense heat generated during metal production processes.
- Q: What are the typical properties of monolithic refractories used in iron and steel industry?
- Monolithic refractories used in the iron and steel industry typically possess high thermal conductivity, excellent resistance to thermal shock, and high mechanical strength. They are also known for their ability to withstand high temperatures and harsh chemical environments. Additionally, these refractories exhibit good erosion and abrasion resistance, low porosity, and high density, making them ideal for lining furnaces, ladles, and other equipment in the iron and steel production process.
Send your message to us
Monolithic Refractories for Iron and Steel Industry:High Alumina Raw Bauxite Products
- Loading Port:
- Qingdao
- Payment Terms:
- TT OR LC
- Min Order Qty:
- 400 m.t.
- Supply Capability:
- 5000 m.t./month
OKorder Service Pledge
OKorder Financial Service
Similar products
Hot products
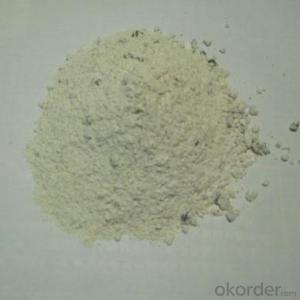
Monolithic Refractories for Iron and Steel Industry - Acid Ramming Mass for Induction Furnace Lining
Hot Searches
Related keywords