Fiberglass Mesh Ceramic Filter Plate
- Loading Port:
- China Main Port
- Payment Terms:
- TT OR LC
- Min Order Qty:
- -
- Supply Capability:
- -
OKorder Service Pledge
Quality Product, Order Online Tracking, Timely Delivery
OKorder Financial Service
Credit Rating, Credit Services, Credit Purchasing
You Might Also Like
Fiberglass mesh filter for molten aluminum filtration are designed and woven for the diffusion and filtration of molten aluminum.The molten aluminum is very easy to be oxidated when touch with air.With the use of NX-EFG,the pure molten aluminum is more easy to get during primary melting, foundry casting and scrap recycling.The main type can be the one without coating or Acrylic coating(white color) or with resin coating(yellow color) and non-smoke treatment(black color).
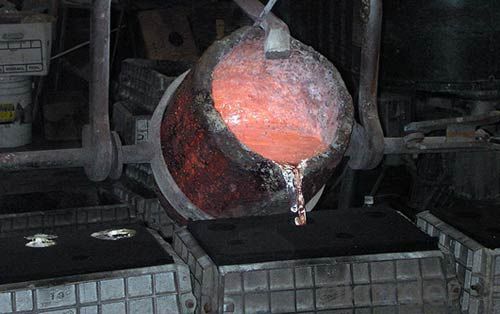
Main Features:
-No contaminate to the molten aluminum
-Cost effective & easy installation
-Reduce turbulence & improve distribution and flow
-Remove oxides and inclusions.
-Excellent stiffness and toughness,good impact resistance
-Well organized grid to ensure fine filtration
Application:
-As the first filtration for primary smelting
-Sand casting,gravity or low pressure die casting
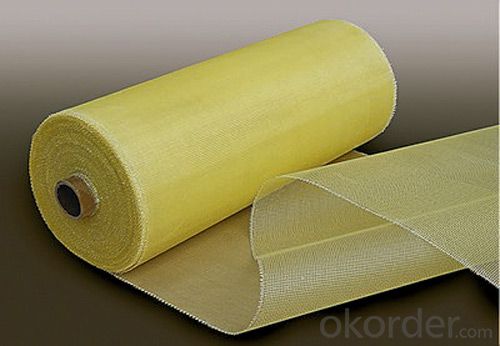
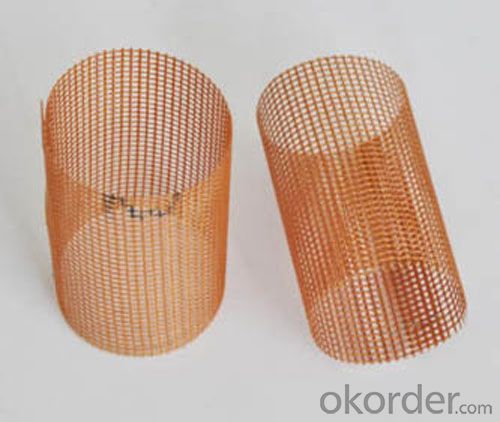
Specification:
Yarn type:Alkali free E-glass
SiO2 contents:58%
Weave pattern:Leno or plain
Weight:50-400g/m2
Width:Max.2.10m
Length per roll:50/100/150/200/300m or as per request
Mesh size:0.5-2.5mm
Open area:25-65%
Thickness:0.18-35mm
Working temperature:700-850 Degree C
*Mesh size:1.0x1.0mm,1.2x1.2mm,1.5x1.5mm,2.0x2.0mm,2.5x2.5mm.
*Different cut pieces sizes and shapes like cap,tubular,funnel etc. are available upon request.
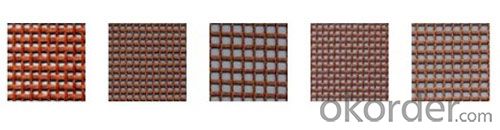
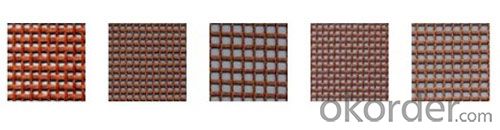
- Q: The ceramic filter suddenly did not smoke, and later he was all right. What's the reason?
- How old the general ceramic filter suction main reason mud cake thickness is not much of a ceramic filter plate is different, because the ceramic filter backwash water, vacuum suction and nitrate are through the distribution valve, are often the same boat". See your description, you do not know the 5 line is about "5 disc or sideways 5 rows of ceramic plates, that is completely not suction or suction effect is poor, I hope to help you:
- Q: The ceramic filter plate is broken. What will happen to the vacuum pump?
- That's a good question. I hope my answer will help you.Ceramic filter ceramic plate broken, nothing more than ceramic plate plug and ceramic plate rupture, you should be the problem of ceramic plate rupture.
- Q: What are the materials that make up the ceramic mold?
- From the development trend of rice, the development of ceramic membrane preparation technology mainly in the following 2 aspects: one is the porous membrane research, to further improve the already commercialized inorganic ultrafiltration and microfiltration membrane, nanofiltration membrane with molecular sieve, the development function of gas separation membrane and pervaporation membrane: two in dense membrane research solid electrolyte membrane, ultra-thin metal and its alloy film and ion conduction ability is research hotspot. The commercial porous membranes are mainly ultrafiltration and microfiltration membranes, and their preparation methods are mainly particle sintering and sol-gel. The former is mainly used for making microporous filter membranes, and commercial A1203 films are prepared by particle sintering method.
- Q: The efficiency of ceramic filter is low. What's wrong with it?
- CleanThe cleaning of ceramic filter is divided into two parts: reverse flush cleaning (also useful gas) and combined cleaning. The purpose of cleaning is to discharge the particles from the hole to the ceramic filter board.Anti flushing and cleaning water filter after direct visual pressure can, generally between 0.08--0.12MPa, such as less than 0.05MPa, while the poor flushing effect without even washing effect, resulting in blocking accumulation eventually led to the ceramic filter plate hole plugging scrap. Replacing the filter element in time and ensuring the water pressure before filtration can provide stable backwashing water pressure.Combined cleaning by ultrasonic vibration, nitrate dissolution method for maximum remove blockage of backwash rushed out, the general ceramic filter every 8 hours of continuous work should stop cleaning 1 hours, such as the use of the old plate or the suction effect is poor, can strengthen cleaning (such as shorten the cleaning period, prolong the period of cleaning, increase the amount of nitric acid etc.).
- Q: Ceramic filter fineness thin mud suction is not what to do more
- With ceramic filter to treat pulp dehydration, the particle size is too large, the particles are easy to precipitate, the particle size is too small, too much mud, then the water content of the filter cake will increase, and the life of the ceramic filter plate will be reduced.
- Q: The use of water glass as beneficiation agent, copper concentrate in the ceramic filter can not filter, how to do?
- Of course, there may be equipment operating parameters can not meet the requirements, ceramic filter board has blocked hole close to scrap.Ceramic filter in use in the process of problems, should promptly contact manufacturers, seek help.
- Q: Common troubles of ceramic filter
- (1) low vacuum, can not meet the production requirements. The main reason is the vacuum pipeline leakage, vacuum pump circulating water is not enough, vacuum pump impeller wear and tear, distribution head wear, ceramic filter plate damage, filtrate tank drainage valve is not closed, pulp trough material level is lower;(2) low or fluctuating backwash water pressure. The main reason is the blockage or leakage of the backwash water pipe system and the distribution of head wear;(3) the liquid level of the filtrate tank is high. The main reason is that the circulating water pump impeller or pump shell wear, pressure is insufficient, so that the drain valve can not open or drain valve itself failure, and filter barrels and circulating water pipe between the leakage;
- Q: How can I avoid the backwash pressure in the production of ceramic filter?
- Recoil of the ceramic filter is on the clean water under certain pressure, from the inside out flushing blockage blockage in the ceramic filter plate on the internal pore water pressure, the recoil is generally less than 0.12MPa, the pressure is too small or no recoil recoil effect is not good.
- Q: Ceramic filter suddenly do not smoke, a little later on their own good, what reason?
- The size of ceramic filter is generally on both sides of the vacuum tank, such as 50 square meters with 5 square meters of ceramic filter / ring ceramic filter plate combination (possible), there are 10 discs, the ceramic plate left a vacuum tank on the left of the 5 disc for filtration, vacuum filtration tank for the ceramic plate on the right right of the 5 disc. If a vacuum system temporarily fails, it may cause poor suction, no suction, and a normal operation at the other end.
- Q: How should the static and dynamic sealing points of the ceramic filter be leaking?
- When the ceramic filter works, the operation may be as follows: 1. The feed is injected and the pulp is injected into the tank of the ceramic filter. 2, mixing system, ceramic filter stirring rake back and forth mixing, driven by mixing reducer. 3, spindle rotation, material level reached a certain range, through the spindle speed machine to drive the ceramic filter disk rotation.
Send your message to us
Fiberglass Mesh Ceramic Filter Plate
- Loading Port:
- China Main Port
- Payment Terms:
- TT OR LC
- Min Order Qty:
- -
- Supply Capability:
- -
OKorder Service Pledge
Quality Product, Order Online Tracking, Timely Delivery
OKorder Financial Service
Credit Rating, Credit Services, Credit Purchasing
Similar products
Hot products
Hot Searches
Related keywords