Rolled Steel Media Grinding Ball with Top Quality Steel as Raw Material for Mines and Cement Plant
- Loading Port:
- Qingdao Port
- Payment Terms:
- TT or LC
- Min Order Qty:
- 25MTS m.t.
- Supply Capability:
- 200000MTS/Year m.t./month
OKorder Service Pledge
OKorder Financial Service
You Might Also Like
Our advantages of Rolled Steel Media Grinding Ball with Top Quality Steel as Raw Material for Mines and
Cement Plant:
a) State-owned company with good credit
b)high quality products
c)competitive prices
d)timely delivery
e)satisfactory service
Specific Characteristics of Rolled Steel Media Grinding Ball with Top Quality Steel as Raw Material for
Mines and Cement Plant:
1. The overall high hardness: the hardness can reach 55-67HRC, volume hardness reaches 50-63HRC, and the average hardness gradient distribution.
2. The impact toughness can reach 12J/ cm .
3. Low broken rate: crush resistance is the general casting grinding ball 10 times, ball impact more than 20000 times the number, the breakage rate of not more than 1%.
4. No deformation: Forged steel grinding balls not roundness from beginning to the end.
Chemical Elements of Rolled Steel Media Grinding Ball with Top Quality Steel as Raw Material for Mines
and Cement Plant:
Name | C | Mn | Si | Cr | S | P |
CMAX-50MN | 0.48-0.56 | 0.70-1.0 | 0.17-0.37 | 0.25 max | 0.035max | 0.035max |
CMAX-65MN | 0.60-0.70 | 0.90-1.20 | 0.17-0.37 | 0.25 max | 0.035max | 0.035max |
CMAX-75MnCr | 0.70-0.85 | 0.7-0.8 | 0.17-0.37 | 0.7-0.9 | 0.03 max | 0.03 max |
CMAX-40MNCr | 0.45-0.50 | 0.7-1.2 | 0.17-0.37 | 0.9-1.1 | 0.03 max | 0.03 max |
Characteristics: | ||||||
Name | Impact Test | Endurance Test Times | Dia 25mm-60mm | Dia 70mm-100mm | ||
AK.J/cm2 | (5m) | Surface | Core | Surface | Core | |
CMAX-50MN | ≥12 | ≥10000 | ≥56 | ≥50 | ≥55 | ≥50 |
CMAX-65MN | ≥15 | ≥12000 | ≥60 | ≥50 | ≥55 | ≥50 |
CMAX-75MnCr | ≥17 | ≥12000 | ≥60 | ≥52 | ≥60 | ≥50 |
CMAX-40MNCr | ≥16 | ≥12000 | ≥60 | ≥50 | ≥60 | ≥50 |
- Q: What are the requirements for casting steel castings?
- 4 thickness, most should be placed above the.5 and try to reduce the number of.6, the sand core should be used in classification of flat surface
- Q: Why do cheap cars like stamping parts instead of casting parts?
- Separation process is also called blanking, the purpose is to make the stamping parts along a certain contour line from the sheet metal separation, at the same time guarantee the quality requirements of the separation section. Stamping is a highly efficient production methods, the use of compound die, especially the multi station progressive die stamping process can be completed in a multi machine, realized by belt uncoiling, leveling, punching, forming and finishing automatic production. High production efficiency, good working conditions, low production costs, can produce hundreds of parts per minute. The purpose of forming processes is to allow the sheet to undergo plastic deformation without breaking the billet and to make the desired shape and size. In actual production, a variety of processes are often applied to a workpiece. Blanking, bending, shearing, drawing, bulging, spinning, and straightening are the main types of stamping machines.
- Q: It is generally said that cast iron is re smelted by pig iron. My question is..:1 pig iron for melting iron, is directly cast into products (such as bed cover, etc.); or that is just the first pig iron smelting iron casting, such as to cover, bed and other products, will once again cast iron melt to casting?2, there are many castings to the engine. Are these castings made by the engine manufacturer themselves or bought by others?There is no need to answer all. Thank you!!!
- The molten iron (molten iron, scrap steel, scrap casting, iron alloy) is melted into cast iron by means of an electric furnace or cupola, and is poured into a casting.
- Q: What are the casting parts processing engineering?
- Among them, special casting has metal mould casting, pressure casting, low pressure casting, lost wax casting (also known as precision casting), shell casting, lost foam casting, centrifugal casting, continuous casting, V casting, and clay casting
- Q: For example, casting parts contain many holes, inclusions and other defects, the size and the number of holes exceed which limit is not qualified
- According to the grade of the parts, according to the relevant standards, the regular drawings will be noted in the technical requirements of the parts.
- Q: What foundry factories are used in the casting parts of China's major automobile manufacturers?
- This is too muchYou do not have a specific list of statistics, but there are many foundries in china!Moreover, car prices are unlikely to be ordered in the local factories!
- Q: Heat treatment process and purpose of casting parts
- Natural aging (also known as Chang Hua): lost in the open, the sun and rain, can have experienced years of wind and frost.
- Q: Lathe processing stainless steel casting parts to use what type of tool, the speed into the amount of how much tool angle
- Processing stainless steel materials, you can use YG class tools, such as YG8, YG8N. The tool geometric parameters g0=15 degrees to 18 degrees, a0=6 degrees to 8 degrees, kr=75 degrees, ls=-5 degrees to -8 degrees; cutting amount is Vc=43 m/min, ap=0.3 to 0.5 mm, f=0.16mm/r.
- Q: What reason is the bronze statue choking fire?
- The casting process in boiling phenomenon, is the setting of the exhaust hole positioner position or number is not reasonable, the air cavity can not be discharged, overwhelmed by a material inlet, reflux, change mould, sincerely help you look forward to adopt,
- Q: The difference between sheet metal and casting parts
- Casting parts are made by casting (followed by a variety of processing), the shape can be simple, can also be very complex, usually large parts, as a base, bed, work table, and so on, good seismic performance.
1. Manufacturer Overview
Location | Shandong,China |
Year Established | 2000 |
Annual Output Value | US$5 Million - US$10 Million |
Main Markets | Domestic Market, South Asia, Southern Europe, Northern Europe, Central America |
Company Certifications | ISO9001;IS014001 Certificate |
2. Manufacturer Certificates
a) Certification Name | |
Range | |
Reference | |
Validity Period |
3. Manufacturer Capability
a) Trade Capacity | |
Nearest Port | Qingdao Port |
Export Percentage | |
No.of Employees in Trade Department | 10-20 People |
Language Spoken: | English;Chinese; |
b) Factory Information | |
Factory Size: | Above 100,000 square meters |
No. of Production Lines | Above 10 |
Contract Manufacturing | Grinding Balls; Grinding Rods; Grinding Cylpebs. |
Product Price Range | Average |
Send your message to us
Rolled Steel Media Grinding Ball with Top Quality Steel as Raw Material for Mines and Cement Plant
- Loading Port:
- Qingdao Port
- Payment Terms:
- TT or LC
- Min Order Qty:
- 25MTS m.t.
- Supply Capability:
- 200000MTS/Year m.t./month
OKorder Service Pledge
OKorder Financial Service
Similar products
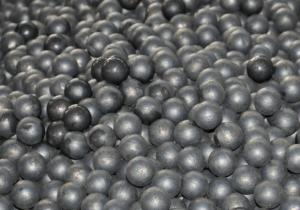
Forged Grinding Media Steel Balls With High Hardness and Resistance, Top Quality For Cement and Mine
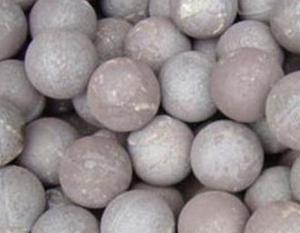
High Chromium Cast Grinding Ball with Top Quality Steel as Raw Material withch can be uesed in Mines
Hot products
Hot Searches
Related keywords