Pre-painted Galvanized/Aluzinc Steel Sheet Coil with Prime Quality and Best Price in Blue color
- Loading Port:
- Shanghai
- Payment Terms:
- TT or LC
- Min Order Qty:
- 50 m.t.
- Supply Capability:
- 10000 m.t./month
OKorder Service Pledge
OKorder Financial Service
You Might Also Like
With GI (aluzinc) as base metal, after pretreatment (degrease and chemical treatment) and liquid dope with several layers of color, then after firing and cooling, finally the plate steel is called pre-painted galvanized (aluzinc) steel.
Pre-painted galvanized steel is good capable of decoration, molding, corrosion resistance.
It generally displays workability, durability and weather resistance.
1.Main Features of the Pre-painted Galvanized/Aluzinc Steel Coil
• Excellent corrosion resistance
• Excellent weather resistance
• Capability of decoration, molding, corrosion resistance
• Workability, durability
• Excellent heat resistance performance
• High strength
• Good formability
• Good visual effect
2.Pre-painted Galvanized/Aluzinc Steel Coil Images 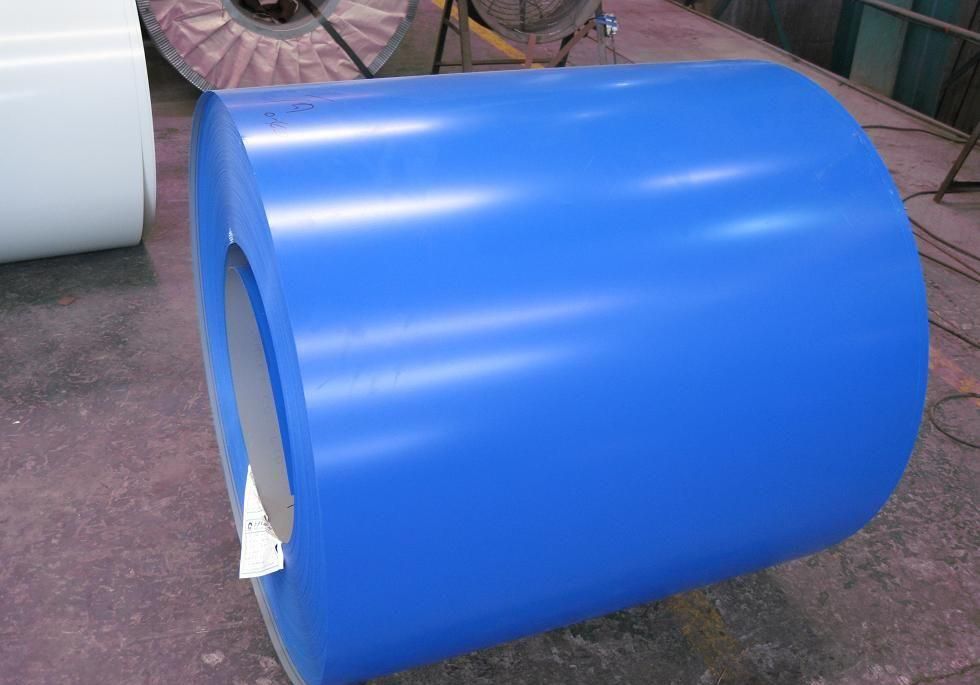
3.Pre-painted Galvanized/Aluzinc Steel Coil Specification
Quality Standard | JIS G3312 CGCC & CGLCC |
Hardness of P | Both soft and hard quality are available |
Surface Finish | with or without protect film |
Thickness | 0.14-1.20 mm |
Width | 914mm, 1000mm, 1220mm and 1250mm, thickness 600-1250mm is available |
Finish by Coil or Sheet | Both sheet and coil are available |
Zinc Coating | 60-275G/M2, both sides |
Paint Thickness for top side | 5 micron primer + (10-20) microns modified polyester, blue color code. |
Paint Thickness for back side | (5-10) microns Epoxy |
Weight per Coil | 4-6 tons, also can be upon customer's requirements |
Max Loading Weight in one 20ft container | 25 tons generally |
4. FAQ of Pre-painted Galvanized/Aluzinc Steel Coil
We have organized several common questions for our clients,may help you sincerely:
1) What is the minimum order quantity ?
Our MOQ is 50mt for each size.
And we will consider to give more discount if you make big order like 1000 tons and more.
Further more, the more appropriate payment term your offer the better price we can provide.
2) How long can we receive the product after purchase?
Usually within thirty working days after receiving buyer’s advance payment or LC.
We will arrange the factory manufacturing as soon as possible.
The cargo readiness usually takes 15-25 days, but the shipment will depend on the vessel situation.
- Q: What are the common methods of preserving steel coils?
- Some common methods of preserving steel coils include applying protective coatings, such as oil or paint, to prevent corrosion and rust formation. Another method is using VCI (Vapor Corrosion Inhibitor) paper or film, which releases chemicals that prevent oxidation. Additionally, steel coils can be stored in climate-controlled environments or wrapped in moisture-resistant materials to minimize exposure to moisture and humidity, which can accelerate corrosion.
- Q: 3 bedroom rambler with attached garage. A bad hail storm in May damaged my white siding and roof. I am concerned insurance adjustThanks much.er will not give me replacement value for steel siding. Any one know the cost and where to buy in Minnesota.
- they both cost around the same
- Q: Suppose you made a sword out of diamond (just follow me here, it's only theoretical). Would it be lighter than a sword of the same size made out of steel?
- Diamond has half the density of steel but would make a terrible sword because it is not very tough. Toughness is a material's ability to resist breakage from forceful impact: Diamond has a toughness of 2.0 MPa·m1/2 and has a critical stress intensity factor of 3.4 MN·m?3/2. That makes it tough for a gem but are poor compared with steels. Plus diamond has a cleavage plane.
- Q: Are steel pokemon weak against any attacks? If so, what types? (like water, grass, etc.)
- I believe a fire pokemon wins against a steel.
- Q: I have hundreds of pounds of scrap steel... who purchases this steel and what is the price per pound etc. of this? Does someone pick it up or do I bring it somewhere?
- It okorder /
- Q: I want to buy a machete made of 1055 carbon steel, and want to know if this steel is durable for repeated use, or even combat use.
- This Site Might Help You. RE: What is the level of dependability of 1055 carbon steel? I want to buy a machete made of 1055 carbon steel, and want to know if this steel is durable for repeated use, or even combat use.
- Q: Having a new kitchen and would like to know the pros and cons of stainless steel as opposed to white appliances. I can only think of finger marks on the SS, which I believe are difficult to remove. Anyone had both that they could advise please?
- Like others said about Stainless Steel, plus if bleach accidentally touched it, it will leave a permanent scar, Stainless Steel can be cleaned with water and soap then with baby oil. White will be better.
- Q: What are the challenges in coil leveling for high-strength steel?
- One of the main challenges in coil leveling for high-strength steel is the material's inherent strength and hardness. High-strength steel is designed to have superior mechanical properties, which can make it difficult to manipulate and flatten during the leveling process. The high tensile strength and increased yield strength of the steel can cause it to resist deformation, leading to springback or permanent deformation issues. Additionally, the increased hardness of the steel can put more strain on the leveling equipment, potentially leading to wear and tear. Proper equipment selection, precise control of leveling parameters, and advanced process monitoring techniques are required to overcome these challenges and achieve accurate and consistent coil leveling results for high-strength steel.
- Q: How are steel coils used in the production of metal signage?
- Steel coils are an essential component in the production of metal signage. These coils are typically made from high-quality steel and come in various thicknesses and widths. The use of steel coils allows for efficient and cost-effective manufacturing processes. To begin, steel coils are unwound and fed into a machine called a roll former or a metal press. This machine shapes the steel into the desired form and design for the signage. The coils' ability to be easily manipulated and shaped makes them ideal for creating intricate and customized signage designs. Once the steel has been formed, it can undergo various processes to enhance its appearance and durability. For instance, the steel may be coated with a layer of paint or powder coating to protect it from corrosion and provide a visually appealing finish. This coating can also be customized to match specific branding or design requirements. After the steel has been shaped and coated, it can be further processed to add features such as embossing or perforations. These additional details can enhance the overall aesthetic appeal of the metal signage and make it stand out. Furthermore, steel coils offer excellent structural integrity, ensuring that the metal signage remains strong and durable even in harsh environmental conditions. This durability is particularly crucial for outdoor signage that needs to withstand exposure to weather elements such as rain, wind, and sunlight. In summary, steel coils play a vital role in the production of metal signage. Their versatility, durability, and ease of manipulation make them an ideal material for creating customized designs. Whether it's for indoor or outdoor use, steel coils provide the necessary strength and aesthetic appeal required for high-quality metal signage.
- Q: What are the different types of steel coil surface finish treatments?
- There are several different types of steel coil surface finish treatments available, each serving a specific purpose and providing unique characteristics. Some common types include: 1. Hot Rolled: This is the most basic and common type of steel coil surface finish treatment. It involves heating the steel above its recrystallization temperature and then rolling it to achieve the desired thickness. This process results in a rough surface texture. 2. Cold Rolled: Unlike hot rolled, cold rolled steel coil undergoes a process where it is rolled at room temperature. This treatment produces a smoother surface finish with improved dimensional accuracy and tighter tolerances. 3. Galvanized: Galvanization is a process where a protective zinc coating is applied to the steel coil surface. This treatment not only enhances the appearance but also provides excellent corrosion resistance, making it suitable for outdoor applications. 4. Electro-galvanized: Similar to galvanized steel, electro-galvanized steel coil is coated with a zinc layer. However, the coating is applied through an electroplating process, resulting in a thinner and more controlled coating. 5. Pre-painted: Pre-painted steel coil surface finish treatment involves applying a layer of paint or other protective coating before the product is delivered to the customer. This treatment enhances the appearance and provides additional protection against corrosion. 6. Stainless Steel: Stainless steel coil surface finish treatment involves passivating the steel to remove any impurities or contaminants on the surface. This process improves the resistance to corrosion and gives the steel a clean and smooth appearance. 7. Embossed: Embossing is a surface finish treatment where a pattern or design is pressed into the steel coil surface. This treatment enhances the aesthetics of the product and can provide additional grip or texture depending on the specific design. 8. Brushed: Brushing is a treatment where a fine abrasive material is used to create a brushed pattern on the steel coil surface. This finish provides a unique texture and can help mask scratches or other imperfections. These are just some of the various types of steel coil surface finish treatments available. The choice of treatment depends on the specific requirements of the application, such as appearance, corrosion resistance, or functionality, and it is important to select the most appropriate treatment to ensure the desired outcome.
Send your message to us
Pre-painted Galvanized/Aluzinc Steel Sheet Coil with Prime Quality and Best Price in Blue color
- Loading Port:
- Shanghai
- Payment Terms:
- TT or LC
- Min Order Qty:
- 50 m.t.
- Supply Capability:
- 10000 m.t./month
OKorder Service Pledge
OKorder Financial Service
Similar products
Hot products
Hot Searches
Related keywords