Dedusting Equipment of Electric Furnace
- Loading Port:
- China Main Port
- Payment Terms:
- TT OR LC
- Min Order Qty:
- -
- Supply Capability:
- -
OKorder Service Pledge
OKorder Financial Service
You Might Also Like
Dedusting Equipment of Electric Furnace
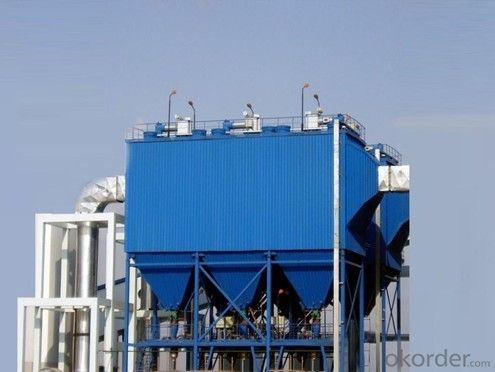
Furnace flue gas capture technology
At present, the mature method of furnace flue gas capturing are semi-closed cover type and diversion roof cover type. The diversion roof cover is actually combined by one semi-closed hood and roof cover.
△ Semi-closed cover
The semi-closed is composed of fixed cover and movable cover, the movable cover can remove to the top of transformer. Semi-closed cover is widely used in dust removal system of medium and small electric furnaces in recent years. Compared with roof cover, its advantages are: the system drafting amount is smaller, flue gas collection efficiency is higher, investment and operating costs are relatively low. Semi-closed cover can completely capture the flue gas during furnace smelting, however, its capturing efficiency of flue gas produced material loading and unloading is not satisfied and opening, closing of the semi-closed cover has certain impact for the smelting period.
△Diversion roof cover
The diversion roof cover is composed of diversion cover and roof cover.
The diversion cover is composed of fixed cover and movable cover, the former is installed at material unloading side and at the back of furnace, while the latter is installed at the top of transformer behind furnace. The movable diversion cover will be moved to the top of transform during material feeding and be moved out of furnace proper during smelting. The fixed and movable diversion covers surround electric furnace, forcing the flue gas arising within the diversion cover area. After flue gas rises to the diversion cover hole, the distance between gas and cover is only 5m, which minimize the bad effect of transverse flue gas. After commissioning, the movable cover can be fixed and only be moved during maintenance so as to decrease operation procedures. The roof cover is inner and outer double layers structure. The inner cover will collect the flue gas flowed out from diversion cover along diffusion corner, while the outer cover will collect the overflowed flue gas.
The diversion roof cover can remove flue gas produced in smelting, which is environmental friendly and easy to be operated, but the disadvantages are that air discharging amount is large and investment, operation cost is high.
Flue gas collection technology of LF furnace
For the present, the mature methods of furnace flue gas capturingare semi-closed covertype and furnace cover type. The structure of semi-closed coveris same with that of electric furnace. The furnace cover is that the top of water cooling furnace cover of LF furnace is equipped with one round gas exhausting cover, which spares electrode incoming and outgoing holes in the middle position, the furnace cover and electrode moves simultaneously. Another kind of furnace cover is that gas exhausting pipes are connected to the sides of water cooling furnace cover. There is 100mm space between furnace cover and gas exhausting pipe.
Flue gas flow produced during LF furnace smelting is not large, which can be eliminated by the furnace cover, besides, the dedusting system is of low investment and operation cost.
Flue gas collection technology of AOD furnace
Compared with the common converter, AOD converter has the following characteristics: long smelting time, low oxygen blowing intensity, low decarburization speed and low CO content; therefore the flue gas recovery of AOD converter is .of little value.
Flue gas of AOD converter is collected bythe movable cover. The cover top is made of stainless steel plate and the cover inner wall is painted with refractory material. The CO-containing flue gas produced during smelting, fully combusts with induced air at the furnace hole, resulting high temperature flue gas up to 900 ~ 1600 ℃. AOD converter will produce certain dust during feeding and steel solution unloading. At the mean time, the high temperature flue gas should be cooled down by mixed air, so that AOD converter is specially equipped with the secondary dust collection device, which uses diversion roof cover, and mix the secondary flue gas with roof exhaust gas.
Performance comparison of various dust collector
| Furnace cover | Rotarycover | Large closedcover | Roof cover | Traveler passing cover |
Gas discharging outside of the furnace | Processed | Processed | Processed | Processed | Processed |
Gas discharging inside of the furnace | Not processed | Processed | Processed | Not processed | Not processed |
Dust collection rate | 50% | 70% | 95% | 40% | 85% |
Whole process collection | Poor | Poorer | better | good | good |
Affect the operation | Poor | Poor | better | good | good |
Occupied space | Small | smaller | bigger | big | big |
Endurable capacity | Poor | Poorer | better | good | good |
Noiseand heat radiation proof | Poor | Better | good | poor | poor |
Air flow dealing | Small | Medium | Large | Highe | Large |
Installation cost | Low cost | Medium | High | Highest | Higher |
Operation cost | Low cost | Medium | High | Highe | Higher |
Dedusting system process:
Specifications of AE series baghouse
Model | Air dealing volume (m3/h) | Filtering area | Filtration velocity (m/min) | Operation resistance (Pa) | Emission concentration (mg/m3) | Inlet temp (℃) | Volume | Total weight | Ash cleaning gas pressure | Air consu |
AE1 | 10000 | 210-140 | 0.8-1.2 | 1000-1500 | 15-50 | 100-250 | 8000 | 4200-6250 | 0.4-0.6 | 2.5-3 |
AE5 | 50000 | 700-1050 | 0.8-1.2 | 1000-1500 | 15-50 | 100-250 | 9000 | 21000-31250 | 0.4-0.6 | 2.5-3 |
AE10 | 100000 | 1400-2100 | 0.8-1.2 | 1000-1500 | 15-50 | 100-250 | 9000 | 42000-62500 | 0.4-0.6 | 2.5-3 |
AE20 | 200000 | 2800-4200 | 0.8-1.2 | 1000-1500 | 15-50 | 100-250 | 14000 | 83000-125000 | 0.4-0.6 | 2.5-3 |
AE-40 | 400000 | 5600-8300 | 0.8-1.2 | 1000-1500 | 15-50 | 100-250 | 23000 | 167000-250000 | 0.4-0.6 | 2.5-3 |
AE60 | 600000 | 8300-12500 | 0.8-1.2 | 1000-1500 | 15-50 | 100-250 | 37000 | 250000-375000 | 0.4-0.6 | 2.5-3 |
AE-80 | 800000 | 11100-16700 | 0.8-1.2 | 1000-1500 | 15-50 | 100-250 | 50000 | 333000-500000 | 0.4-0.6 | 2.5-3 |
AE-100 | 1000000 | 13900-21000 | 0.8-1.2 | 1000-1500 | 15-50 | 100-250 | 58000 | 416700-625000 | 0.4-0.6 | 2.5-3 |
AE-120 | 1200000 |
- Q: What is the difference between industrial furnaces and boilers?
- A boiler is a mechanical device for heating water into hot water or steam by the use of heat from fuel or other sources of energy. The original meaning of a pot is a water container heated by fire. The furnace is the place where the fuel is burned. The boiler includes two parts, the cooker and the furnace.
- Q: Heat treatment equipment (industrial furnace), which products generally contain what kind of, which industries need to use heat treatment industrial furnace equipment.
- The main equipments of heat treatment are classified into two major categories: main equipment and auxiliary equipment. The main equipment includes heat treatment furnace, heating device, surface modification, surface oxidation device, surface mechanical enhancement device, cooling equipment, cold processing equipment, process parameter detection and control instrument; auxiliary equipment includes cleaning cleaning equipment, furnace atmosphere heating medium permeability meter preparation equipment, cooling device, quenching medium heavy transport machinery, quality testing equipment, power transmission line and auxiliary equipment, fire safety equipment, dust and other production fixture.
- Q: What are the companies in the world that are currently engaged in metallurgical furnaces?
- Each manufacturer has its own industry and technological advantages.If you say that the performance rankings, turnover, and so on, it seems that no one has done this ranking.
- Q: What are the combustion equipments used in industrial boilers?
- Main auxiliary equipment for general boilers:1. domestic appliances 2. civilian gas boiler 3. industrial gas furnace.
- Q: What is industrial furnace masonry?
- Masonry industrial furnaces refers to complete materials such as brick kilns in construction process.
- Q: What are the advantages of a vacuum furnace?
- Energy consumption is lower than salt bath furnace. Modern advanced vacuum industrial furnace heating chamber is made of high quality heat insulation material and wall, which can concentrate electric heating energy into heating chamber with remarkable energy saving effect.
- Q: What is the difference between industrial furnace masonry and ordinary masonry?
- Industrial furnace masonry requirements are relatively high, industrial furnaces of different uses, whether material or masonry process, have strict requirements.
- Q: Brief introduction to repair of industrial furnace
- Although the number of industrial furnaces in general machinery plants is not large, the number of large repairs per year accounts for 16%-20% of the total number of repairs for all equipment, and the large repair costs account for about 18%-25% of the total repair cost of all equipment.
- Q: What is the difference in structure between industrial furnace and boiler?
- At the same time, the working environment is relatively poor, the structure should be sturdy and durable, the transfer mechanism (generally) to stable and durable low failure rate, the insulation layer must be thick enough and the economy, the steel structure housing materials used to be enough.
- Q: What is an industrial furnace pit?
- In twentieth Century 50s, coreless induction furnaces were developed rapidly. Later, electron beam kilns, using electron beams to impact solid fuels, strengthen the surface to heat and fuse materials with high melting point.
Send your message to us
Dedusting Equipment of Electric Furnace
- Loading Port:
- China Main Port
- Payment Terms:
- TT OR LC
- Min Order Qty:
- -
- Supply Capability:
- -
OKorder Service Pledge
OKorder Financial Service
Similar products
Hot products
Hot Searches
Related keywords