Blast Furnace Pulverized Coal Injection
- Loading Port:
- China Main Port
- Payment Terms:
- TT OR LC
- Min Order Qty:
- -
- Supply Capability:
- -
OKorder Service Pledge
OKorder Financial Service
You Might Also Like
Blast Furnace Pulverized Coal Injection
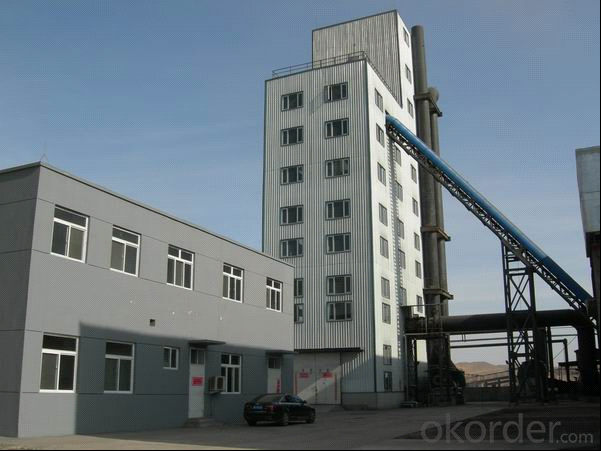
Blast furnace pulverized coal injection technology has become a main measure for coke saving, iron increasing and improving smelting effect and facilitating blast furnace operation smoothly, also has become blast furnace smelting technological progress and main method in today's world
Blast furnace pulverized coal injection replaces heat provided by carbon inside coke, enriches reductive gas inside furnace and improves indirect reduction. Due to cooling effect to furnace hearth, temperature along with the hearth radium direction distributed evenly which has provided the condition for blast furnace receiving blast temperature and improved pig iron quality.
During blast furnace pulverized coal injection, it must ensure that coal injection should be safely, reliable and continuously in order to reduce iron-making cost. Therefore, realizing of continuously automatic injection is a main problem that needs to be considered under the condition of control safety and reliability has been guaranteed.
Technical Significance
Blast furnace pulverized coal injection has a revolutionary significance to blast furnace iron-making technology, which is a key technology to decide whether blast furnace could compete with other iron making methods and to continuous survival and development, thereby the significance is specified as below:
(1) By using low cost pulverized coal to replace expensive and gradually scarce metallurgical coke that will reduce blast furnace iron-making coke ratio and pig iron cost.
(2) Coal injection is effective means to adjust furnace condition heat system.
(3) Pulverized Coal injection can improve working condition of blast furnace hearth and make blast furnace operate smoothly.
(4) The injected pulverized coal is gasified and burnt before tuyere that will reduce the theoretical combustion temperature, in order to maintain the necessary T theory of blast furnace smelting; it needs compensation, which has created a condition for blast furnace using high blast temperature and oxygen enrichment blast blowing.
(5) More hydrogen emitted than coke during the process of coal injection gasification, which improved gas reducing capacity and penetration diffusivity capacity, and will be in favour of ore reduction and improved blast furnace operation index.
(6) Partial metallurgical coke is replaced by coal injection that will mitigate the requirement of coking coal, reduce coking facilities and save construction investment, especially for partial coking furnace that had been operated 30 years and required overhaul, quantity demanded of coke will be reduced due to coke replaced by pulverized coal, the coking furnace that required to be overhaul should shut down and abandon.
(7) Coke replaced by injected pulverized coal will reduce coking furnace quantity and coke yield, thus, it will also lower the environment pollutions caused by coking.
Our Advantages
1. According to different requirements and characteristics of user, it can achieve personalized customization of process proposal, including single series paratactic double tanks, single series paratactic three tanks, single and double series chain tanks, double series five tanks, paratactic six tanks, one set of injection tank corresponding with two blast furnaces and other coal injection processes.
2. Strict Process Control Proposal
2.1 Technological process and control requires the blast furnace pulverized coal injection system mainly including raw coal storage and transportation system, coal pulverizing system, drying system and injection system.
2.2 The raw coal storage and transportation system, the raw coal is conveyed through belt conveyor to soft coal bunker and anthracite bunker,according to total coal feeding quantity and soft coal and anthracite proportion to set and achieve automatic coal blending in coal pulverizing workshop. Technical process control requirement of raw coal storage and transportation system: to achieve automatic coal blending as per technical process control requirement.
2.3 The coal pulverizing system drying agent is absorbed into medium-speed mill through negative pressure formed by main exhaust blower, the raw coal will be evenly added into medium-speed mill through weighing coal feeder, after the raw coal is crushed and dried, qualified pulverized coal will be entered into bag-type powder collector through pulverized coal piping, it will be stored in pulverized coal bunker after collecting. Technical process control requirement of coal pulverizing system: to achieve automatic regulation for medium-speed mill inlet pressure, system air volume and temperature.
2.4 The drying agent in drying system is a mixture gas of high temperature flue gas in flue gas furnace and low temperature flue gas in blast furnace and hot blast heater. Technical process control requirement of drying system: to achieve automatic regulation for air and gas volume proportion required when flue gas furnace combusting.
2.5 Injection system adopts high pressure juxtaposition type injection tank to convey pulverized coal for blast furnace. Technical process control requirement of injection system: to achieve automatic injection as per coal injection volume required by blast furnace.
3. Advanced Automatic Control
The reliable operating high pressure and low pressure drive system, advanced and open computer control system, excellent and smooth man-machine interaction interface. As per the requirements of user, it can use software that user acquainted to control program and design technical process display.
● Steady, advanced, reliable operating high pressure and low pressure drive system
● Electric, instrument and computer “Three electrical”integrated to be one control mode.
● Abundant technical parameter, all sort of operating and controlling measures are equipped ,real time dynamical man-machine interaction interface.
● Safe and reliable, all inspected security interlock and alerting system
● A combination operating mode between integrated interlock control and local control maintenance.
● Standard and orderly cable laying.
4. Comprehensive Service
We can design coal injection system to customer.
We can provide whole set of all mechanical equipments, electric equipments, and automatic control and production tools in coal injection workshop to customer.
We can provide EPC contract to customer: including whole sets of workshop design, civil construction, equipment manufacture and whole sets of equipment installation, commissioning, trial run and production operation service.
- Q: What is the difference between industrial furnaces and boilers?
- Hot water or steam generated in the boiler can directly provide necessary energy for industrial production and people's life, but also by the steam power device is converted to mechanical energy, or through the generator converts mechanical energy into electrical energy. Hot water boilers are called hot water boilers. They are mainly used in daily life, and are also used in industrial production. Steam generating boilers are called steam boilers, often referred to as boilers. They are used in thermal power stations, ships, locomotives and industrial and mining enterprises.
- Q: Heat treatment equipment (industrial furnace), which products generally contain what kind of, which industries need to use heat treatment industrial furnace equipment.
- The general metal die casting plant and the metal smelting plant need process melting and dissolving furnace, usually there are reverberatory furnace, cupola, rotary furnace, etc. I do the melting furnace of aluminium alloy.
- Q: What are the companies in the world that are currently engaged in metallurgical furnaces?
- There are many kinds of furnaces in metallurgical industry,colored and black,smelting and heat treatment are also included.
- Q: What are the combustion equipments used in industrial boilers?
- The main auxiliary equipments of the general boiler are: upper coal machine, ash blower, blower, draught fan, economizer, feed pump and water treatment unit. Oil boilers are: oil pumps, burners, tanks and so on.
- Q: What is industrial furnace masonry?
- Pre construction and recording shall be carried out on complex and important parts of industrial furnaces,masonry of all kinds of masonry shall be made with staggered joint masonry.
- Q: Why does the burner of industrial furnace burn occasionally?
- The general process for burner ignition, blowing furnace, electric spark ignition, solenoid valve, open the gas in case of delayed spark ignition, detection device detects the flame, the controller accepts signal so that the solenoid valve open, gas continuous normal combustion. However, if the ignition fails or the burner fires, the detector cannot detect the flame, which causes the solenoid valve to close and the burner flameout.
- Q: How many kinds of industrial electric furnaces are there?
- Electric furnace is divided into four categories: resistance furnace, induction furnace, arc furnace and special electric furnace according to the different ways of electric heating.
- Q: What is the difference between industrial furnace masonry and ordinary masonry?
- Furnace industry is not generally Mason walls, needs to have a professional operation and rich construction experience, high level of industrial furnace is difficult to get.
- Q: How to use industrial furnace equipment?
- When the furnace is used, the lifting mechanism of the furnace door must be in good condition, and the wire breakage of the steel wire is not allowed to exceed the designated value. The weight should be properly allocated, and the drive department shall be provided with a protective cover.
- Q: Brief introduction to repair of industrial furnace
- The working condition of industrial furnace is very bad. It is affected by high temperature, slag erosion and burden wear. Therefore, its working condition changes quickly and its service life is short.
Send your message to us
Blast Furnace Pulverized Coal Injection
- Loading Port:
- China Main Port
- Payment Terms:
- TT OR LC
- Min Order Qty:
- -
- Supply Capability:
- -
OKorder Service Pledge
OKorder Financial Service
Similar products
Hot products
Hot Searches
Related keywords