Alumina Ceramic Foam Filter Plate for Molten Aluminium
- Loading Port:
- China Main Port
- Payment Terms:
- TT OR LC
- Min Order Qty:
- -
- Supply Capability:
- -
OKorder Service Pledge
Quality Product, Order Online Tracking, Timely Delivery
OKorder Financial Service
Credit Rating, Credit Services, Credit Purchasing
You Might Also Like
APPLICATION:For the filtration of molten aluminum and non ferrous alloy.
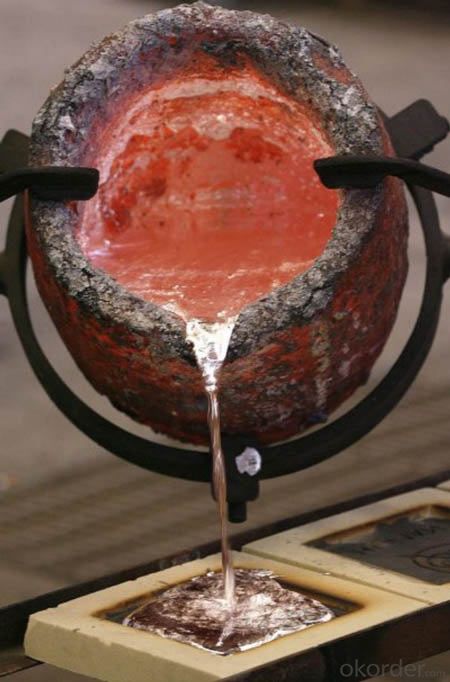
Alumina Ceramic Foam Filters mainly for filtration of aluminum and alloys in foundries and cast houses .With the excellent
resistance to attack and corrosion from molten aluminum, the filter can effectively remove inclusions, reduce trapped gas
and provide laminar flow and then the filtered metal is significantly cleaner.Cleaner metal results in higher-quality castings,
less scrap, and fewer inclusion defects, all of which contribute to bottom-line profit.
resistance to attack and corrosion from molten aluminum, the filter can effectively remove inclusions, reduce trapped gas
and provide laminar flow and then the filtered metal is significantly cleaner.Cleaner metal results in higher-quality castings,
less scrap, and fewer inclusion defects, all of which contribute to bottom-line profit.
-Reduce scrap related to inclusions.
-Reduce costs related to inclusion defects.
-Increase productivity with higher extrusion or rolling speeds.
-Increase casting flexibility with easy alloy changes.
-No holding metal.
FEATURES:
*Superior dimensional tolerances
*Stable chemical composition
*Highest filtration efficiency
*Excellent strength
*Resistant to corrosion attack by molten aluminum and alloys
*Beveled edges and compressible gasket
SPECIFICATION:
Color:White
Working Temp :≤1100°C
Porosity:80~90%
PPI(pores per inch):10/20/30/40
PPI(pores per inch):10/20/30/40
Compression Strength (Room Temperature) :≥0.8Mpa
Volume Density: 0.36-0.5g/cm3
Thermal Shock Resistance:1100°C to room temperature 6 times
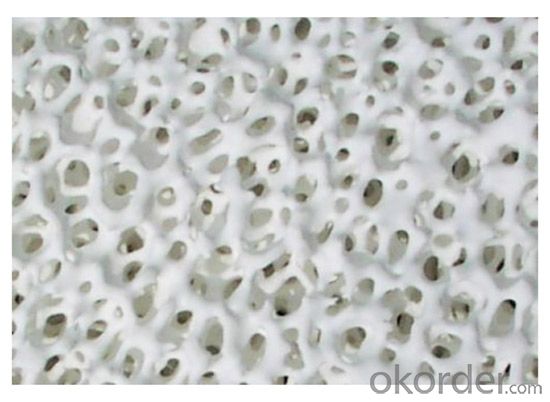
COMMON SIZES:
7x7x2" (178x178x50mm)
9x9x2" (229x229x50mm)
12x12x2" (305x305x50mm)
15x15x2" (381x381x50mm)
17x17x2" (432x432x50mm)
20x20x2" (508x508x50mm)
23x23x2" (584x584x50mm)
7x7x2" (178x178x50mm)
9x9x2" (229x229x50mm)
12x12x2" (305x305x50mm)
15x15x2" (381x381x50mm)
17x17x2" (432x432x50mm)
20x20x2" (508x508x50mm)
23x23x2" (584x584x50mm)
*Other sizes can be customized upon request.
- Q: What filter material are placed in the aquarium filter?
- Generally let off the filter cotton and ceramic rings, there are biochemical balls, coral bone, stone, activated carbon and so onConditional: filter cotton, ceramic ring, biochemical ball, coral bone, stone, activated carbon
- Q: The ceramic filter suddenly did not smoke, and later he was all right. What's the reason?
- The size of ceramic filter is generally on both sides of the vacuum tank, such as 50 square meters with 5 square meters of ceramic filter / ring ceramic filter plate combination (possible), there are 10 discs, the ceramic plate left a vacuum tank on the left of the 5 disc for filtration, vacuum filtration tank for the ceramic plate on the right right of the 5 disc. If a vacuum system temporarily fails, it may cause poor suction, no suction, and a normal operation at the other end.
- Q: Working principle, ultrasonic trouble and troubleshooting of ceramic filter
- It is based on the action principle of capillary pore and realizes the solid-liquid separation through the capillary action principle of the micropore. Specifically, is the use of microporous ceramic plate water impermeable properties, extraction of ceramic plate and external cavity vacuum pressure, the suspended material groove under the action of the negative pressure adsorption on the ceramic plate, solid material through the porous ceramic plate can not be trapped in a ceramic plate surface, and the liquid due to the hydrophilic effect of vacuum pressure difference and ceramic plate by entering the gas-liquid distribution device, and then discharged or recycled, so as to achieve the purpose of solid-liquid separation.
- Q: Ceramic filter in vacuum pressure enough, the ceramic plate does not suck pulp, what is the reason for analysis?
- The filtrate is not discharged smoothly.The filtrate can not be discharged in a timely and smooth manner, the new filtrate can not be sucked out, and the filtrate can not be continuously sucked out, so that the filter cake can not be adsorbed on the ceramic plate.
- Q: What is the filtration accuracy of 50nm ceramic membrane?
- 50nm refers to the nominal pore size, but it does not mean that the holes in the ceramic membrane are 50nm, but the approximate number of holes. The size of the pores may be between 40~60 and 45 to 55nm. Generally introduced, annotated range, you can also own to detect.
- Q: What are the materials that make up the ceramic mold?
- Ceramic membrane, also known as CT film, is one of the solid membrane, the earliest by Japan's large Japanese printing company and Toyo ink company in 1996, the introduction of the market. The ceramic coating is mainly A12O3, Zr02, Ti02 and Si02 of inorganic materials such as porous membrane preparation, the pore size of 250mm. Has good chemical stability, acid resistance, alkali resistance, solvent resistance, high mechanical strength, can reverse flushing: anti microbial ability: high temperature, narrow pore size distribution, higher separation efficiency characteristics, has been widely used in food industry, biological engineering, environmental engineering, chemical industry, petroleum chemical industry, metallurgy industry etc. The market sales, with an annual growth rate of 35% growth. Compared with plastic products of ceramic membrane with similar high cost, but also has many advantages, it is hard to withstand strong, durable, not easy to have chemical resistance village, invasive and high temperature liquid cleaning liquid has a stronger ability to resist, its main drawback is the price expensive. _ complex manufacturing process
- Q: How much is the accuracy of 50nm ceramic membrane filtration?
- 50nm refers to the nominal pore size, but it does not mean that the holes in the ceramic membrane are 50nm, but the approximate number of holes. The size of the pores may be between 40~60 and 45 to 55nm. Generally introduced, annotated range, you can also own to detect.
- Q: Ceramic filter capacity.
- You ask too general, to say processing capacity (ie capacity), at least to provide material conditions, such as: material name, concentration, particle size distribution. In addition, the basic conditions of equipment operation should be taken into account.
- Q: What's the acid of the ceramic filter plate?
- Ceramic filter automatic control system: control system through the metering pump will be concentrated nitric acid automatic mixing ceramic filter plate into nitrate after proportioning through the pipeline, so that it can be dissolved, dredge the blockage in the most microporous ceramic filter plate. This is the ceramic filter plate pickling, pickling, acid dosage should be sufficient as little pickling effect.
- Q: What is the backwashing pressure of the ceramic filter?
- Ceramic filter is a kind of solid-liquid separation, dehydration drying equipment, such as dehydration pulp, mortar. The backwash of ceramic filter is to flush the filter medium (ceramic filter plate) with clean water with a certain pressure.
Send your message to us
Alumina Ceramic Foam Filter Plate for Molten Aluminium
- Loading Port:
- China Main Port
- Payment Terms:
- TT OR LC
- Min Order Qty:
- -
- Supply Capability:
- -
OKorder Service Pledge
Quality Product, Order Online Tracking, Timely Delivery
OKorder Financial Service
Credit Rating, Credit Services, Credit Purchasing
Similar products
Hot products
Hot Searches
Related keywords