Cold-Rolled Steel Coil (JIS G3141-1996, EN 10131-2006, DIN EN 1002)
- Loading Port:
- China main port
- Payment Terms:
- TT OR LC
- Min Order Qty:
- 10 m.t.
- Supply Capability:
- 10000 m.t./month
OKorder Service Pledge
OKorder Financial Service
You Might Also Like
Specification
PERIME COLD ROLLED STEEL COIL
Product Description
Specifications of Cold Rolled Steel Coil:
1)Grade: SPCC, SPCD, SPCE, DC01-06, St12, Super deep drawing2)Standard: JIS G3141-1996, EN 10131-2006, DIN EN 1002
3)Thickness: 0.20mm - 3.0mm
4)Width: 600/1000/1250/1500 (mm) or per customer's request
5)Coil ID: 508mm/610mm or per customer's request
Classification:
Classification | Designation | Characteristics | Size(mm) | Main applications |
Commercial quality | SPCC,SPCCT | Commercial quality suitable for bending fabrication and simple forming; this is the type in greatest demand. | Thickness 0.18-3.0 Width 600-1500 | Refrigerators, cabinets, power distribution boards and drums. |
Drawing quality | SPCD | Drawing quality second only to that of SPCEN. Excellent uniformity. | Thickness 0.18-2.0 Width 600-1250 | Automobile floor and roof panels. |
Deep-drawing quality | SPCE,SPCF | Deep-drawing quality. With metallurgically controlled grain size, it retains its beautiful finish even after being deep-drawn. | Thickness 0.18-2.0 Width 600-1250 | Automobile fenders and quarter panels |
Chemical Components:
Grade | Chemical Components | ||||
C | Mn | P | S | Alt | |
SPCC | ≤0.12 | ≤0.50 | ≤0.035 | ≤0.025 | ≥0.020 |
SPCD | ≤0.10 | ≤0.45 | ≤0.030 | ≤0.025 | ≥0.020 |
SPCE | ≤0.08 | ≤0.40 | ≤0.025 | ≤0.020 | ≥0.020 |
Mechanical Properties:
Grade | Strengh | ||||
YS | TS | Elongation(%) | |||
MPA | δ | S | P | ||
SPCC DC01 | 130-260 | 270-410 | 28 | ||
SPCD DC03 | 120-240 | 270-390 | 34 | ||
SPCE SPCEN | <210 | 270-370 | 38 | ||
DC04 DC05 | <210 | 270-370 | 38 | ||
AISI 1006 | 275-365 | 275-380 | 34 | 32 | 30 |
AISI 1008 | 275-390 | 275-410 | 32 | 30 | 28 |
AISI 1010 | 295-410 | 295-430 | 30 | 29 | 28 |
AISI 1020 | 355-490 | 355-500 | 26 | 25 | 24 |
AISI 1045 | 530-685 | 16 | |||
AISI 1050 | 540-715 | 14 | |||
AISI 1060 | 550-775 | 12 | |||
ST33 S185JR | 185-195 | 315-430 | 33 | ||
ST37 S235JR | 215-235 | 375-500 | 25 | ||
ST37 S355JR | 275-325 | 510-680 | 18 |
Thickness Tolerance:
Thickness (mm) | Tolerance allowed(mm) |
0.20-0.50 | +/-0.05 |
0.50-0.65 | +/-0.06 |
0.65-0.90 | +/-0.07 |
0.90-1.00 | +/-0.09 |
1.10-1.20 | +/-0.10 |
1.20-1.40 | +/-0.12 |
1.40-1.50 | +/-0.13 |
1.50-1.80 | +/-0.14 |
1.80-2.00 | +/-0.15 |
2.50-3.00 | +/-0.20 |
Width Tolerance:
Width(mm) | Tolerance allowed (mm) |
≤200 | +2.0/-1.0 |
>200-300 | +2.5/-1.0 |
300-400 | +3.0/-2.0 |
400-600 | +3.5/-2.5 |
600-1000 | +6/-0 |
>1000 | +10/-0
|
- Pickling: To clean the dust and rust points on the surface.
- Cold Rolling: Digital rolling control system produces minimum thickness tolerance, helps to prevent twist and improve straightness.
- Slitting: Precise slitting machinery helps control the best width tolerance and avoid camber or cracker. Also we can make round or sharp edge with additional process and special machines.
- Heat treatment: Advanced annealing, tempering and hardening techniques will help to produce proper mechanical property of the products to insure our client's usage with minimum harm to natural environment.
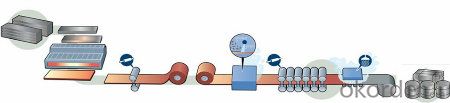
1) For the further producing of hot dip galvanized steel products
2) Cold rolled Steel Coil: Auto manufacture, Oil drum, Transformer's tank panel, Furniture etc.
- Q: What are the factors affecting the strength of steel coils?
- The factors affecting the strength of steel coils include the composition of the steel, the manufacturing process used, the temperature and time of heat treatment, the presence of impurities or defects, and the degree of deformation during processing.
- Q: What is the maximum tension that steel coils can withstand during uncoiling?
- The maximum tension that steel coils can withstand during uncoiling depends on various factors such as the specific grade and thickness of the steel, the diameter and weight of the coil, and the handling equipment used. Generally, steel coils can withstand tension levels ranging from a few hundred pounds to several thousand pounds. It is crucial to consider manufacturer guidelines and industry standards to ensure safe and efficient uncoiling operations.
- Q: I bought stainless steel appliances a year ago. I have two kids who like to put their hands all over the fridge and they always leave dirty marks all over it. I bought stainless steel cleaner but it doesn't do a good enough job. Anyone know any other cleaning remedies?
- All the stainless steel cleaners I've tried are fine for polishing, but they don't clean anything. A damp microfiber towel (the kind with loops like terry cloth) does a good job. You might be able to use plain water because the cloths are so good. Or mix up some dish soap in water and wet the towel with that. You can use windex if you want something more convenient.
- Q: How are steel coils stored?
- Steel coils are typically stored in warehouses or outdoor storage yards. They are usually stacked on top of each other in a crisscross pattern to maximize space utilization and prevent them from rolling. Additionally, steel coils may be secured with steel banding or placed on pallets to ensure stability during storage and transportation.
- Q: What are the different methods of oiling steel coils?
- There are several methods of oiling steel coils, including applying oil by roll coating, using a spray system, or immersing the coils in an oil bath.
- Q: What are the common coil thickness tolerances?
- The common coil thickness tolerances can vary depending on the specific industry and application. However, typical tolerances for coil thickness range from +/- 0.001 inches to +/- 0.005 inches.
- Q: Where can a find a steel scrubber. Its great to clean cooking vessels. Would be great if someone gives me an idea. I did not find it at CVS, but was in a hurry, will try again tomorrow.
- Are you talking about steel wool? You should be able to find that at Wal*Mart or Target. If they don't carry it, I would recommend looking for a kitchen supplies store in a phonebook.
- Q: What are the challenges in coil blanking for complex shapes?
- Coil blanking for complex shapes presents several challenges that need to be addressed in order to achieve accurate and efficient results. One significant challenge lies in the precise positioning and alignment of the coil material. Complex shapes often require intricate cutting patterns, and any misalignment or deviation can lead to inaccurate cuts and wasted material. Another challenge is the selection and optimization of the blanking tooling. Complex shapes often require specialized dies and punches, which need to be carefully designed and manufactured to ensure accuracy and consistency. This not only involves the selection of appropriate tooling materials but also the consideration of factors such as cutting forces, wear resistance, and tool life. The complexity of the shapes also poses challenges in terms of material deformation and springback. During the blanking process, the material undergoes various deformations and stresses, which can cause distortions and dimensional variations in the final product. Achieving the desired shape while minimizing these deformations requires a thorough understanding of material properties and advanced techniques such as compensation and adjustment in the die design. Furthermore, the high-speed nature of coil blanking for complex shapes can lead to increased vibration and noise levels. The dynamic forces involved in cutting intricate shapes can result in tool chatter and excessive noise, which not only affects the quality of the cut but also the overall operational efficiency. Implementing effective damping and vibration control measures, such as tool coatings and optimized cutting parameters, is crucial to mitigate these challenges. Lastly, the complexity of the shapes can also impact the overall production efficiency. Complex shapes often require longer tool setup times and more frequent tool changes, which can lead to increased downtime and reduced productivity. Additionally, the intricate nature of the cuts may require multiple passes or additional machining operations, further adding to the production time and complexity. To overcome these challenges, manufacturers need to invest in advanced technologies, such as computer-aided design and simulation software, to optimize the blanking process. Additionally, continuous research and development efforts focused on improving tooling materials, cutting techniques, and process control can help address the challenges associated with coil blanking for complex shapes.
- Q: I am building a robot for Bots IQ. In doing so i have the option of building the the armor of my robot out of titanium or tool steel.. which would be the better option.Brief description of Bots IQ: It is a competition where 2 15lb robots go and attack each other with spinning blades, hammers or whatever is designed.
- Titanium is a significantly stronger and lighter metal, but is also extremely expensive. If you have the option for titanium, go for it.
- Q: how do i quinch steel? i heard instead of water oil will actually make it harder... wat ways are best for wat steels? and how do i tell wat kind of steel i have?... i will be doin this with my poket knife..
- boy what a though question ! let me explain. when you rapidly cool a steel from high temperatures(depending on steel type) with water or oil or other means , it is called quenching. it depends on the steel type to say if it is better to quench it with oil or water but basically in water you will have a harder steel rather than oil. for some steels if you do this you will ruin it's properties ! you can't totally tell what kind of steel do you have until you get it analyzed with Quantometer analyzer with a pocket knife it is more like an estimation and it can't be trust able generally if you can scratch the steel with your knife it means it is not a hard steel and it might not be expensive. I hope that helps but for more information i need to know more !
Send your message to us
Cold-Rolled Steel Coil (JIS G3141-1996, EN 10131-2006, DIN EN 1002)
- Loading Port:
- China main port
- Payment Terms:
- TT OR LC
- Min Order Qty:
- 10 m.t.
- Supply Capability:
- 10000 m.t./month
OKorder Service Pledge
OKorder Financial Service
Similar products
Hot products
Hot Searches
Related keywords