Welded Black Carbon Square Tubes Pre-galvanized/ Galvanized ASTM A500 10*10-400*400 Structure Pipe
- Loading Port:
- Tianjin Port
- Payment Terms:
- TT or L/C
- Min Order Qty:
- 50MT m.t.
- Supply Capability:
- based on order m.t./month
OKorder Service Pledge
OKorder Financial Service
You Might Also Like
1. Specification of Hollow Section-Square Tubes
1) Application: Widely used in building, machine, chemical equipment, automobile industrial, container, and also applied to agriculture and mine machine.
2)Standard:ASTM A500, GB6728
3)Steel grade: ASTM A500: A, B, C; GB6728:Q195,Q215,Q235,Q345
4)Delivery Time: 7-20 Days after receving prepayment or L/C
2. Size of Hollow Section-Square Tubes
SIZE(mm) |
THICKNESS(mm) |
10×10 |
0.6-1.0 |
12×12 |
0.6-1.0 |
16×16 |
0.6-1.2 |
19×19 |
0.6-1.5 |
20×20 |
1.6-1.5 |
25×25 |
1.0-2.75 |
30×30 |
1.0-2.75 |
32×32 |
1.0-3.0 |
38×38 |
1.0-3.0 |
40×40 |
1.0-3.5 |
50×50 |
1.0-5.0 |
60×60 |
1.0-6.0 |
63.5×63.5 |
1.0-6.0 |
70×70 |
1.5-6.0 |
75×75 |
1.5-6.0 |
80×80 |
2.0-6.0 |
90×90 |
2.0-6.0 |
100×100 |
2.3-6.0 |
120×120 |
4.0-6.0 |
125×125 |
4.0-6.0 |
150×150 |
4.0-8.0 |
200×200 |
6.0-12 |
250×250 |
6.0-12 |
300×300 |
6.0-12 |
400×400 |
6.0-12 |
*Remark: Besides below sizes, we also can arrange production based on requirement of customer's requirement
3. Packing&Delivery
Packing Details: Big OD: in bulk; Small OD: packed by steel pipe;Plastic bags 4 or According to customer's requirement
Delivery Time: 20-30 days upon receving prepayment or L/C
4. Data Sheet
ASTM A 500
Chemical Requirement | |||||
Composition % | |||||
Grade A |
Grade B | ||||
Element |
Heat analysis |
Product analysis |
Heat analysis |
Product analysis | |
Carbon max |
0.26 |
0.3 |
0.22 |
0.26 | |
Manganese max |
… |
… |
1.4 |
1.45 | |
Phosphorus, max |
0.035 |
0.045 |
0.03 |
0.04 | |
Sulfur max |
0.035 |
0.045 |
0.02 |
0.03 | |
Copper, when copper steel is specified, min |
0.20 |
0.18 |
0.2 |
0.18 | |
Where an ellipsis (...)appears in this table, there is no requirement | |||||
For each reduction of 0.01 percentage point below the specified maximum for carton, and increase of 0.06 percentage point above the specified maximum for manganese is permitted, up to a maximum of 1.50% by heat analysis and 1.6% by product analysis |
Tensile Requirement | ||
|
Grade A |
Grade B |
Tensile strength, min, psi (Mpa) |
48000 (400) |
70000 (483) |
Yield strength, min, psi (Mpa) |
36000 (250) |
50000 (345) |
Elongation in 2 in. (50.8mm), min, % |
23 |
23 |
5. Products Showroom
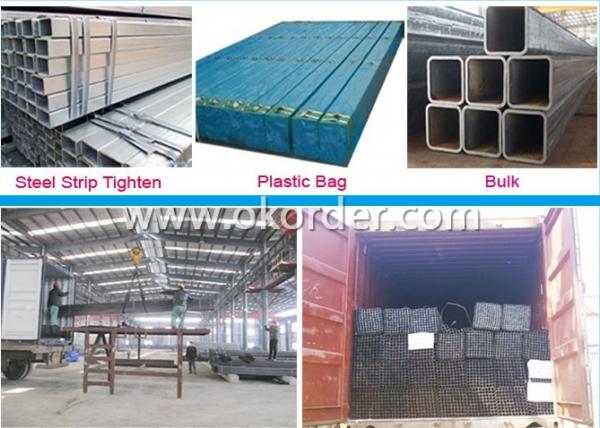
- Q: How are steel pipes used in the construction of dams and water reservoirs?
- Steel pipes are commonly used in the construction of dams and water reservoirs due to their durability, strength, and ability to withstand high pressure and heavy loads. These pipes are utilized in various important aspects of dam and reservoir construction. One of the main uses of steel pipes in these structures is for the transportation of water. Steel pipes are used to convey water from the source, such as a river or stream, to the reservoir or dam. These pipes are designed to withstand the high water pressure and ensure that there is a continuous flow of water to the reservoir. The durability of steel pipes allows them to remain intact even in harsh conditions and environments. In addition to transporting water, steel pipes are also used for drainage purposes. They are used to create drainage systems that help regulate the water level in the reservoir or dam. These pipes are strategically placed to control the flow of water and prevent any potential flooding or overflow. Steel pipes are also used in the construction of the spillways and outlets in dams and reservoirs. Spillways are designed to release excess water from the reservoir during heavy rainfall or when the water level is too high. Steel pipes are used in the construction of these spillways to provide a controlled path for the water to flow out of the reservoir, preventing any damage to the dam or surrounding areas. Furthermore, steel pipes are utilized in the construction of penstocks, which are large pipes that transport water from the reservoir to the turbines in a hydropower plant. The pressure generated by the water in these pipes is used to drive the turbines and generate electricity. The strength and durability of steel pipes are crucial for ensuring the smooth and efficient operation of hydropower plants. Overall, steel pipes play a vital role in the construction of dams and water reservoirs. Their durability, strength, and ability to withstand high pressure make them an ideal choice for various aspects of these structures, including water transportation, drainage systems, spillways, and penstocks.
- Q: Can steel pipes be threaded?
- Yes, steel pipes can be threaded. Threading is a common process used to create screw-like ridges on the ends of the steel pipes, allowing them to be easily connected to fittings or other pipes.
- Q: How are steel pipes used in the construction of underground parking structures?
- Steel pipes are used in the construction of underground parking structures for various purposes, such as providing structural support, drainage, and ventilation. They are commonly used as piles or caissons to support the weight of the structure and prevent it from sinking into the ground. Additionally, steel pipes are utilized for the installation of drainage systems to prevent water accumulation and ensure the structural integrity of the parking structure. They are also employed for ventilation purposes, allowing fresh air to circulate and remove any potentially hazardous gases. Overall, steel pipes are essential components in the construction of underground parking structures, ensuring their stability, safety, and functionality.
- Q: Can steel pipes be used for sewage and wastewater systems?
- Yes, steel pipes can be used for sewage and wastewater systems. Steel pipes are highly durable, resistant to corrosion, and can withstand high pressure and temperature conditions, making them suitable for transporting sewage and wastewater efficiently and securely. Additionally, steel pipes have a long lifespan and can handle the abrasive nature of sewage and wastewater, making them a reliable choice for such systems.
- Q: What is the outer diameter of the steel tube?
- The outer diameter refers to the maximum diameter including the thickness of the steel tube, the inner diameter is the length of the hollow part inside, and the outer diameter minus the inside diameter is the thickness of the steel pipe
- Q: Can steel pipes be used for high-temperature applications?
- Yes, steel pipes can be used for high-temperature applications. Steel is known for its excellent strength and durability, making it suitable for handling high temperatures. However, the specific grade of steel used and the operating conditions must be considered to ensure it can withstand the desired temperature range without compromising its structural integrity.
- Q: What is the maximum length of a steel pipe?
- The maximum length of a steel pipe can vary depending on various factors such as the manufacturing process, transportation constraints, and practical limitations. However, steel pipes can typically be manufactured and transported in lengths ranging from a few meters to several hundred meters.
- Q: What is the difference between steel pipe and polyethylene pipe?
- Steel pipe and polyethylene pipe are utilized for plumbing and construction purposes, but they differ in terms of their materials and characteristics. Steel pipe derives its strength and durability from a combination of iron and carbon. It is commonly employed in industrial settings or for underground gas and oil pipelines where high pressure and heavy loads are expected. Steel pipe is renowned for its corrosion resistance and ability to withstand extreme temperatures. In contrast, polyethylene pipe is a plastic pipe crafted from either high-density polyethylene (HDPE) or low-density polyethylene (LDPE). It is lightweight, flexible, and easy to install, making it a popular choice for residential plumbing and irrigation systems. Polyethylene pipe can resist chemicals, UV rays, and abrasive materials, making it suitable for both above-ground and underground installations. Another notable distinction between steel pipe and polyethylene pipe is their respective costs. Steel pipe is generally more expensive due to the raw materials and manufacturing processes involved. Conversely, polyethylene pipe is relatively affordable and cost-effective, especially for smaller-scale projects. Regarding maintenance, steel pipe necessitates periodic inspections and maintenance to prevent corrosion and ensure durability. Conversely, polyethylene pipe is virtually maintenance-free due to its resistance to corrosion and chemical degradation. To summarize, the primary differences between steel pipe and polyethylene pipe lie in their composition, strength, durability, cost, and maintenance requirements. The choice between these pipes depends on the project's specific needs, considering factors such as pressure, load, budget, and environmental conditions.
- Q: What are the different methods of insulating steel pipes?
- There exists a variety of methods for insulating steel pipes, depending on the specific needs and requirements of the application. Some commonly utilized methods include: 1. Insulation wraps: By enveloping the steel pipes with insulating materials such as fiberglass, mineral wool, or foam insulation and securing them tightly with adhesive or tape, insulation wraps offer a cost-effective and straightforward installation option favored by many. 2. Insulation coatings: Applying a layer of insulating material directly onto the surface of the steel pipe, insulation coatings made from materials like epoxy, polyurethane, or polyethylene protect against corrosion and temperature fluctuations, making them ideal for harsh environments. 3. Insulation jackets: Utilizing pre-fabricated insulation jackets designed to fit over the steel pipes, this method combines insulation materials with a weatherproof outer layer. Insulation jackets are commonly employed for outdoor or exposed pipelines, providing excellent insulation and protection against external elements. 4. Insulation foam: Injecting foam insulation into the space between the steel pipe and an outer casing, the foam expands and hardens to create a sealed and well-insulated layer. Apart from preventing heat loss or gain, foam insulation also offers remarkable soundproofing properties. 5. Insulation tapes: Specially designed insulation tapes made from PVC or rubber, possessing good insulating properties, are wrapped around smaller pipes or joints. This flexible and easy-to-apply solution is commonly employed. When selecting the appropriate method to insulate steel pipes, it is crucial to consider factors such as operating temperature, environmental conditions, and specific application requirements. Seeking advice from a professional or insulation specialist can assist in determining the most suitable insulation method for individual needs.
- Q: How are steel pipes used in the manufacturing of pharmaceutical equipment?
- Steel pipes are commonly used in the manufacturing of pharmaceutical equipment due to their durability and resistance to corrosion. They are used to transport fluids, gases, and chemicals within the equipment, ensuring a safe and reliable flow. Steel pipes also provide a high level of cleanliness, which is crucial in pharmaceutical manufacturing to prevent contamination and maintain product quality.
1. Manufacturer Overview
Location | Hebei, China |
Year Established | 1988 |
Annual Output Value | Above One Hundred Million RMB |
Main Markets | Main land; Southeast Asia; Middle East; Africa |
Company Certifications | ISO 9002:2010;API 5L |
2. Manufacturer Certificates
a) Certification Name | |
Range | |
Reference | |
Validity Period |
3. Manufacturer Capability
a) Trade Capacity | |
Nearest Port | Tianjin |
Export Percentage | 30%-50% |
No.of Employees in Trade Department | 201-500 People |
Language Spoken: | English; Chinese |
b) Factory Information | |
Factory Size: | 50,000 square meters |
No. of Production Lines | Above 15 |
Contract Manufacturing | Meicai Metal Trading Co.Ltd |
Product Price Range | Average |
Send your message to us
Welded Black Carbon Square Tubes Pre-galvanized/ Galvanized ASTM A500 10*10-400*400 Structure Pipe
- Loading Port:
- Tianjin Port
- Payment Terms:
- TT or L/C
- Min Order Qty:
- 50MT m.t.
- Supply Capability:
- based on order m.t./month
OKorder Service Pledge
OKorder Financial Service
Similar products
Hot products
Hot Searches
Related keywords